Guía básica para el procesamiento de moldeo por inyección
Guía básica para el procesamiento de moldeo por inyección
Por: CapableMaching
Prefacio:
Esta guía concisa está diseñada para proporcionar una introducción sencilla a los aspectos básicos del moldeo por inyección. Ya sea que sea nuevo en el campo o busque una referencia rápida, esta página cubre los conceptos básicos, el funcionamiento y la optimización de la máquina. El moldeo por inyección es un actor clave en la industria manufacturera, ya que da forma a productos que van desde artículos cotidianos hasta piezas industriales. Esta guía se esfuerza por simplificar la complejidad y proporcionar información práctica sobre procesos de moldeo efectivos y eficientes. Ya sea estudiante, ingeniero o profesional de la industria, esperamos que esta guía sea un recurso útil que le ayude a navegar por el mundo del moldeo por inyección.
Un "ciclo de inyección" puede referirse a diferentes procesos según el contexto, pero un significado común de ciclo de inyección es en el contexto del moldeo por inyección, un proceso de fabricación utilizado para producir piezas de plástico. En el moldeo por inyección, un ciclo de inyección se refiere a la secuencia de pasos que ocurren para producir una sola pieza o producto.
Para comprender el proceso detallado del moldeo por inyección y cómo ajustar los parámetros correspondientes de la máquina de moldeo por inyección, debemos comprender teóricamente cómo fluye el plástico.
Para producir productos de alta calidad, es necesario comprender los detalles del moldeo por inyección proceso y cómo ajustar los parámetros correspondientes de la máquina de moldeo por inyección, lo que requiere que entendamos cómo fluye el plástico en la máquina, lo que a su vez, debemos conocer las teorías y la terminología en esta área.
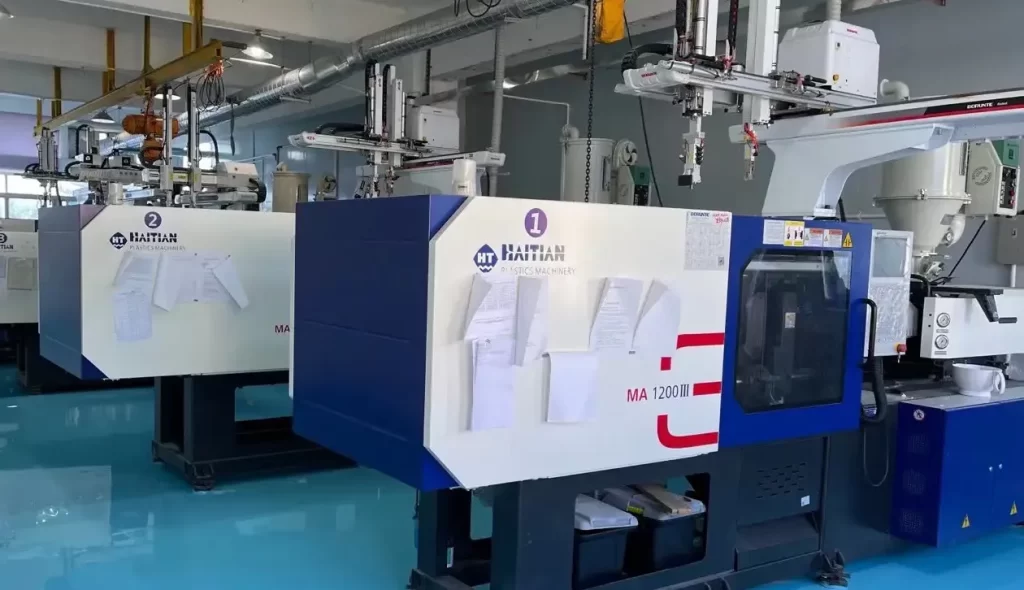
Teoría del flujo de fuente
La teoría del flujo de fuente lleva el nombre de la forma en que el líquido fundido material plástico se comporta cuando entra y llena la cavidad del molde. En esta teoría, se supone que el material plástico fluye hacia el molde de manera similar al flujo de un líquido en una fuente. [1] Aquí hay una explicación simplificada del concepto:
A). Punto de entrada: el material plástico ingresa a la cavidad del molde por un único punto de entrada o por varios puntos de entrada. Este punto de entrada normalmente se llama puerta.
B). Patrón de flujo: a medida que el material se inyecta a través de la compuerta, se mueve hacia afuera y hacia arriba dentro de la cavidad del molde, de manera similar a la forma en que el agua sube y se esparce cuando se bombea un líquido a un punto central, creando un patrón de flujo similar a una fuente.
C). Comportamiento de llenado: el plástico fundido fluye a través de la cavidad del molde, siguiendo este patrón similar a una fuente, y llena los intrincados detalles de la pieza a medida que avanza. Este comportamiento del flujo es fundamental para garantizar que incluso las secciones complejas y de paredes delgadas de la pieza se llenen adecuadamente.
La teoría del flujo en fuente es un concepto importante para los diseñadores de moldes y los ingenieros de procesos en el moldeo por inyección. Comprender cómo fluye el material dentro de la cavidad del molde es crucial para lograr una calidad uniforme de las piezas, minimizar defectos como bolsas de aire o disparos cortos y optimizar los tiempos de los ciclos.
Generalmente, los productos moldeados por inyección son productos planos con un espesor de pared delgado. Un producto plano se define como un producto con un espesor de 3 a 4 mm o menos y un ancho de 5 veces el espesor.[2]
En este tipo de CAVIDAD, la resina fluye y produce una capa solidificada en el molde para formar de antemano un molde que divide el agua.
Según este principio, la resina dosificada en el extremo frontal forma la parte superficial del producto y la resina dosificada en el extremo posterior llena la parte central del producto.
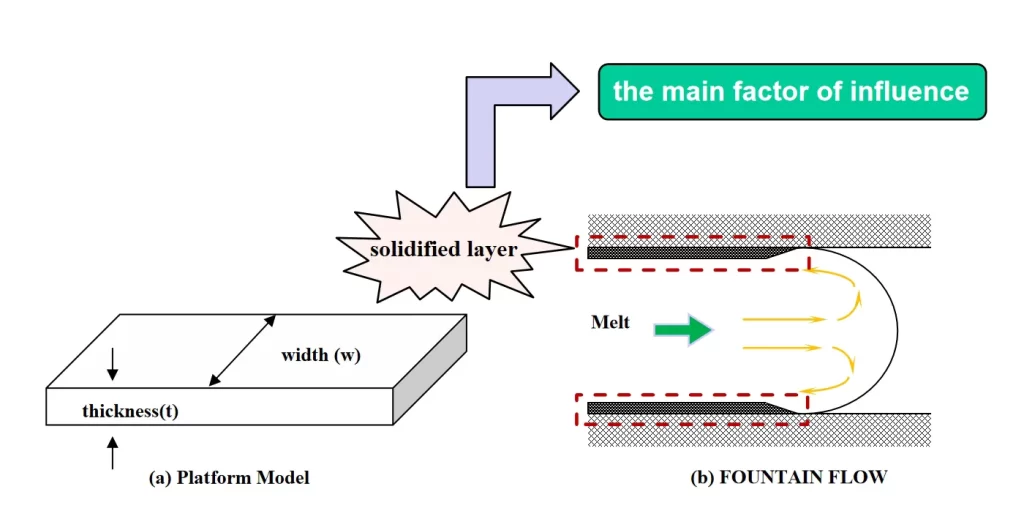
Tasa de deformación por corte y calor de fricción.
La tasa de deformación por corte, a menudo denominada γ (gamma), es un concepto fundamental en reología y mecánica de fluidos que describe cómo las diferentes capas o elementos de un fluido se mueven entre sí, creando corte o deformación dentro del fluido. En el contexto de la teoría del flujo en fuente en el moldeo por inyección, la tasa de deformación por corte es relevante porque ayuda a describir cómo se deforma el material plástico fundido a medida que fluye dentro de la cavidad del molde.
En la teoría del flujo en fuente, la tasa de deformación por corte se refiere a la velocidad a la que las capas o partículas adyacentes del plástico fundido experimentan movimiento relativo o deformación a medida que el material fluye a través de la cavidad del molde. Esta tasa de deformación está influenciada por factores como la velocidad de inyección, la viscosidad del material plástico y la geometría del molde.[3]
Cuando la velocidad de inyección es lenta, a medida que el material ingresa cada vez más al interior del molde, la pérdida de calor es mayor, en este momento, la tasa de deformación por corte se reduce y el calor de fricción generado es menor, el resultado es que la capa de curado de la superficie del producto se vuelve más gruesa, lo que en última instancia afectará el crecimiento del producto.
La velocidad de inyección es rápida, el material ingresa al interior del molde, la pérdida de calor es pequeña, en este momento la tasa de deformación por corte aumenta y el calor de fricción generado aumentará, el resultado es que la superficie del producto de la capa de curado Se vuelve más delgado, pero aumentará el tiempo de enfriamiento del producto, es menos eficiente y, al mismo tiempo, producirá una variedad de defectos (como frentes de lotes), etc.[4]
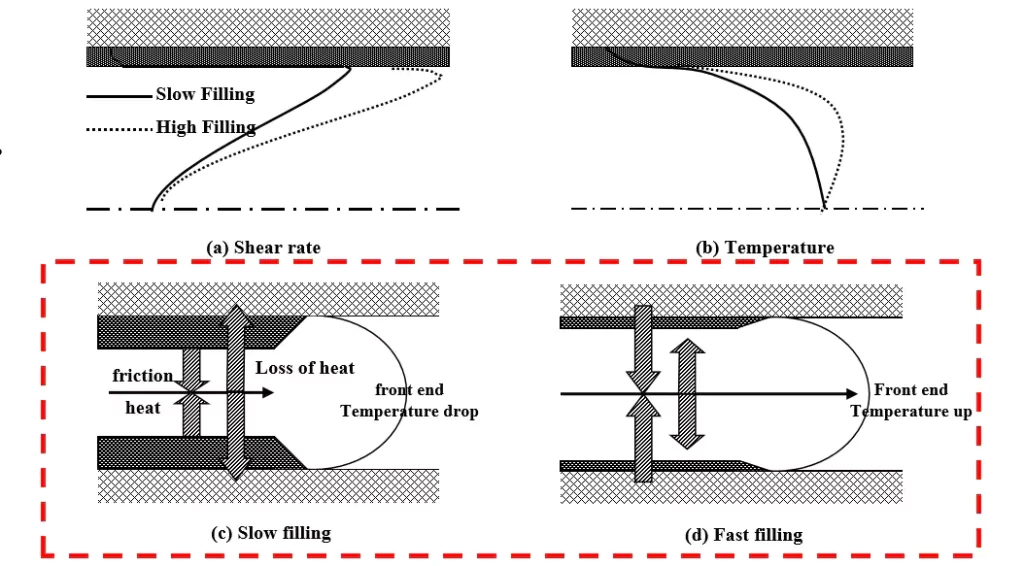
Presión de inyección
La presión de inyección, en el contexto del moldeo por inyección, se refiere a la fuerza o presión aplicada para empujar el material plástico fundido dentro de la cavidad del molde durante la fase de inyección del proceso de moldeo. Es uno de los parámetros clave controlados por la máquina de moldeo por inyección y es un factor crítico para determinar la calidad y consistencia de las piezas moldeadas.
La presión de inyección generalmente se mide en libras por pulgada cuadrada (psi) o megapascales (MPa) y puede variar según factores como el material utilizado, la geometría de la pieza y el diseño del molde.
La magnitud de la presión de inyección requerida depende de varios factores, entre ellos:
a) Viscosidad del material: Los materiales más viscosos (más espesos) requieren presiones de inyección más altas para fluir adecuadamente.
b) Diseño del molde: La complejidad y el tamaño del molde, así como el número y diseño de las cavidades, pueden influir en la presión requerida.
c) Geometría de la pieza: Las piezas de paredes delgadas o intrincadas pueden requerir una presión más alta para llenarse adecuadamente.
d) Velocidad de inyección: Las velocidades de inyección más rápidas a menudo requieren una presión más alta para mantener el flujo.
e) Desde una perspectiva de seguridad, durante la producción, se debe utilizar una presión menor que la presión de inyección máxima de la máquina de moldeo por inyección hasta que se llene el punto final de la cavidad. Generalmente, la presión de inyección es inferior al 80% de la presión de inyección máxima de la máquina de moldeo por inyección.[5]
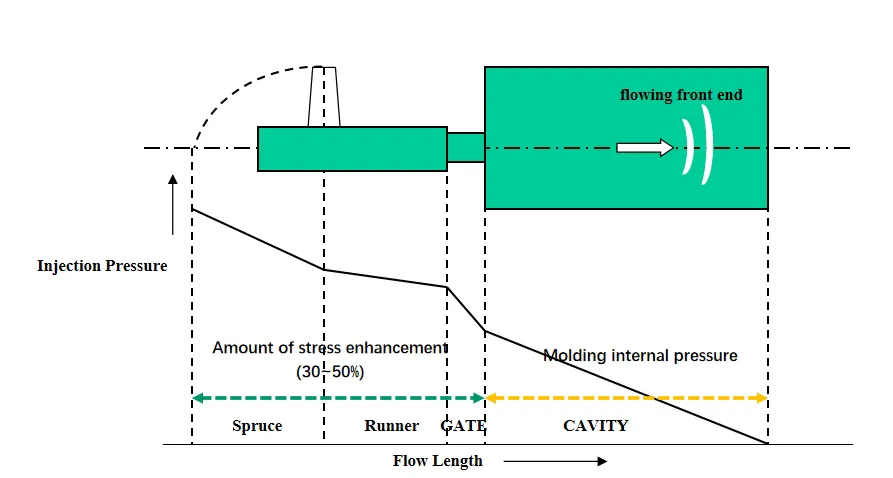
Llenar el tiempo
En el moldeo por inyección, el "tiempo de llenado" se refiere al tiempo que tarda el material plástico fundido en llenar completamente la cavidad del molde durante la fase de inyección del proceso de moldeo. Este parámetro es un aspecto crucial del proceso de moldeo y normalmente se mide en segundos o milisegundos. El tiempo de llenado es uno de los factores clave que influyen en la calidad y consistencia de las piezas moldeadas.
La relación entre la velocidad de inyección y la presión de inyección se muestra en el gráfico como una curva en forma de U. Si la velocidad de inyección es lenta, la pérdida de calor es alta, la temperatura de flujo disminuye, la viscosidad aumenta, el espesor de la capa de curado aumenta, por lo que la resistencia al flujo es alta y la presión de inyección aumenta.
Por el contrario, si la velocidad de inyección es rápida, la temperatura de flujo aumenta, la viscosidad disminuye y el espesor de la capa de curado se vuelve menor. Sin embargo, la resistencia por fricción entre la capa de curado y la capa de flujo aumenta considerablemente, lo que a su vez aumenta la presión de inyección. La presión de inyección se minimiza cuando el caudal en Caviti es constante.[6]
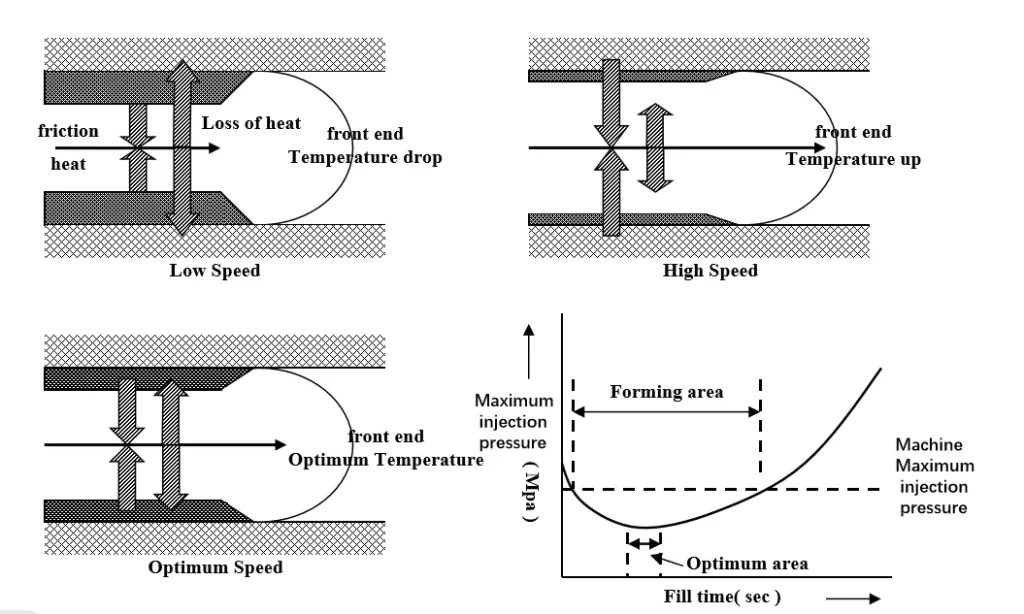
La velocidad de inyección óptima es aquella que minimiza la presión de inyección en las condiciones dadas. Dependiendo del espesor de la cavidad, la velocidad de inyección debe ser diferente. Los delgados tienen una sección de flujo efectiva más pequeña que los gruesos. Por lo tanto, es necesario aumentar la velocidad de inyección, aumentar la tasa de deformación de toda la sección y aumentar la fuerza de deformación por fricción para estabilizar la temperatura del flujo y reducir la presión de inyección. [7]
Dependiendo del material de la resina, el calor específico, la conductividad térmica, la viscosidad, etc. pueden variar mucho. Dependiendo de la temperatura, los materiales con altos cambios de viscosidad (PC, PMMA) tienen un arco en U más pequeño, pero los materiales sin esa propiedad (PP, ABS) tienen un arco en U más grande. Por tanto, algunos materiales son sensibles a la velocidad de inyección y otros no.
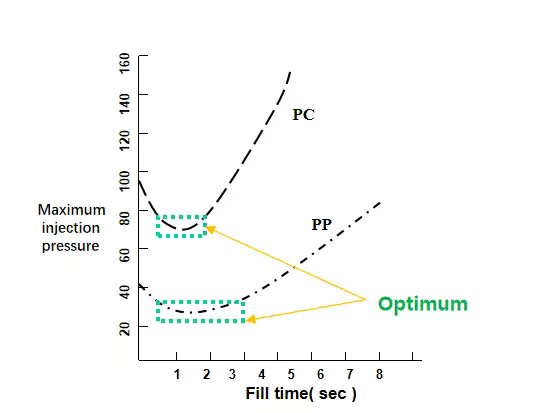
Ajuste de presión de mantenimiento
La presión de retención se refiere a la inyección en el material después de la cavidad para garantizar que la contracción por enfriamiento de la resina no sea demasiado grande, en el momento adecuado para hacer avanzar el tornillo para mantener la presión adecuada en la cavidad, continuar proporcionando la resina. Al proceso de la cavidad, y para compensar el enfriamiento del material plástico fundido que cura la contracción, este proceso tiene un gran impacto en la calidad del producto.
Determinación de la fuerza y el tiempo de retención de la presión.
Fuerza de sujeción: La cantidad de presión de retención determina la cantidad de contracción. Generalmente, si se aumenta la presión de retención, el producto se llenará más y evitará que se contraiga. Si la presión de retención es demasiado baja, el producto disminuirá de tamaño y se producirá una contracción. Sin embargo, una presión de sujeción demasiado alta aumentará la fuerza de forma y la dureza residual, lo que deformará el producto. Generalmente, la presión de mantenimiento adecuada es del 70 al 80 % de la presión de inyección máxima.
Tiempo de presión de mantenimiento: El tiempo de mantenimiento de la presión tiene mucho que ver con el espesor de la cavidad. Debido a que cuanto más espeso es el producto, mayor es el tiempo de enfriamiento, y para evitar la contracción, es necesario suministrar resina todo el tiempo durante ese tiempo, por lo que es necesario mantener la presión durante un cierto período de tiempo. Sin embargo, dado que la resina no puede entrar en la cavidad después de que GATE se haya curado, la presión de retención perderá su efecto óptimo, ya que la resina no puede transmitir presión después de que GATE se haya curado. Aquí, es necesario diseñar el GATE de acuerdo con el espesor del producto para que coincida con el tiempo de mantenimiento; por supuesto, el tiempo de curado del GATE depende del espesor y la longitud del GATE. [8]
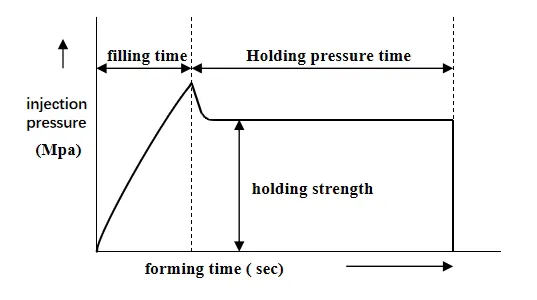
Generalmente, si la presión de retención se aplica uniformemente de acuerdo con una cierta presión, la presión de retención cerca de la PUERTA es grande y la tasa de contracción del producto será pequeña, pero cuando el relleno llega a la parte final, no está suficientemente sujeto a la presión. presión, y la probabilidad de contracción aumenta enormemente y se producirá una contracción desigual. Esta irregularidad aumenta la tensión residual en el producto, que es una causa importante de deformación. Por lo tanto, en lugar de ajustar la presión de mantenimiento a una presión promedio, el tamaño de la presión de mantenimiento se reduce gradualmente y, al ajustar la presión de mantenimiento varias veces, se puede reducir la desviación de la posición de la presión dentro de la CAVIDAD.[9].
Además, también es posible reducir los defectos colocando la PUERTA en la parte gruesa del producto. En términos generales, la tasa de contracción depende de la presión y la velocidad de curado. Configurar GATE en el lugar donde la velocidad de curado es lenta y la tasa de contracción es grande, y proporcionar suficiente presión puede mantener la tasa de contracción dentro de un rango pequeño. En términos generales, el tiempo de mantenimiento de la presión debe establecerse más largo que el tiempo de curado GATE. Si la presión de retención se establece más corta que el tiempo de curado GATE, puede causar que el tornillo retroceda después de la pérdida de presión debido a la resina no endurecida (porque generalmente después del proyecto de presión de retención es el proyecto de medición), y la resina se comprime en el frente de GATE fluirá hacia atrás y luego la tasa de contracción alrededor de GATE será mayor.
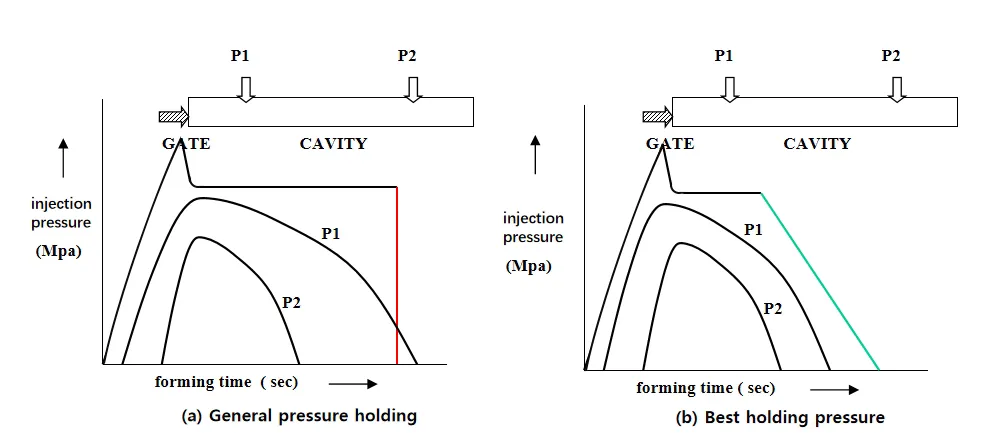
Condiciones de moldeo
Las condiciones de moldeo por inyección se refieren a los parámetros y configuraciones específicos utilizados durante el proceso de moldeo por inyección para producir piezas moldeadas. Estas condiciones juegan un papel crucial en la determinación de la calidad, consistencia y eficiencia del proceso de moldeo. Se consideran varios factores y entornos para lograr resultados óptimos.
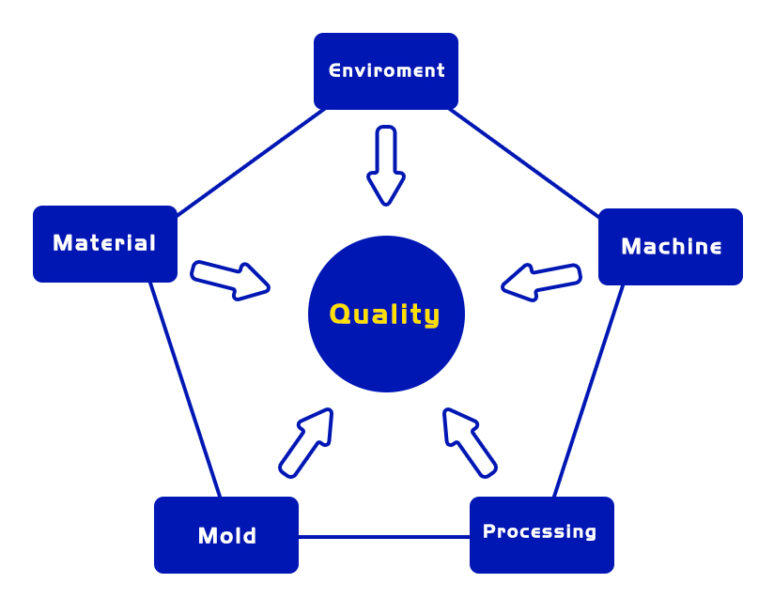
Estas son algunas condiciones clave del moldeo por inyección:
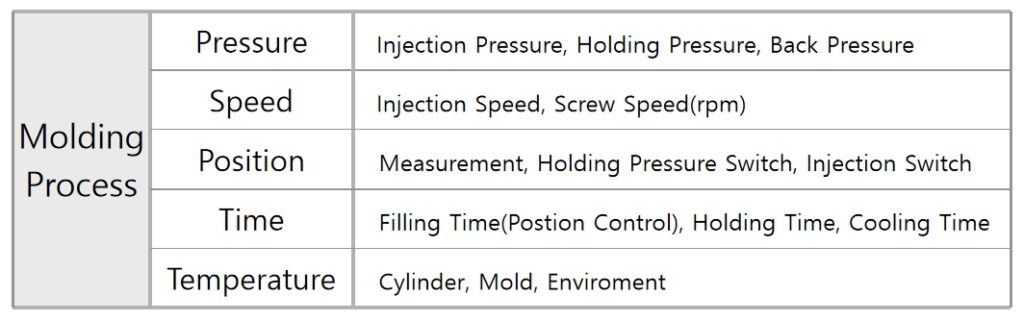
La optimización de estas condiciones de moldeo por inyección requiere una comprensión profunda de las propiedades del material, el diseño de las piezas y las características del molde. Los ingenieros y operadores de procesos ajustan cuidadosamente estos parámetros para lograr la calidad deseada de la pieza y minimizar los defectos durante el proceso de moldeo por inyección. [10]
Aquí debemos explicar algunos términos de uso común.
Cilindro
En el moldeo por inyección, el término "cilindro" normalmente se refiere al cilindro de la máquina de moldeo por inyección. El cilindro de la máquina es un componente crucial donde el material plástico se funde, se mezcla y luego se inyecta en la cavidad del molde para formar la pieza deseada. El barril consta de varias zonas, cada una de las cuales cumple una función específica en el proceso de plastificación.
Temperatura del molde
La temperatura del molde se refiere a la temperatura del molde en el contexto del moldeo por inyección. Es un parámetro crítico en el proceso de moldeo por inyección y tiene un impacto significativo en la calidad y propiedades de las piezas moldeadas. La temperatura del molde se controla cuidadosamente y se mantiene en niveles específicos durante todo el ciclo de moldeo.
Velocidad de inyección
La velocidad de inyección, en el contexto del moldeo por inyección, se refiere a la velocidad a la que se inyecta el material plástico fundido en la cavidad del molde durante la fase de inyección del proceso de moldeo. Es un parámetro crítico que puede afectar significativamente la calidad, apariencia y propiedades de las piezas moldeadas. La velocidad de inyección se mide en milímetros por segundo (mm/s) o pulgadas por segundo (in/s), lo que representa la velocidad de movimiento del tornillo o émbolo de inyección.
Tornillo RPM
Las RPM del tornillo (revoluciones por minuto) en el contexto del moldeo por inyección se refieren a la velocidad de rotación del tornillo dentro de la máquina de moldeo por inyección. El tornillo es un componente clave en el proceso de plastificación, responsable de fundir, mezclar e inyectar el material plástico fundido en la cavidad del molde.
Presión de inyección
Se refiere a la fuerza o presión aplicada para empujar el material plástico fundido hacia la cavidad del molde durante la fase de inyección del proceso de moldeo.
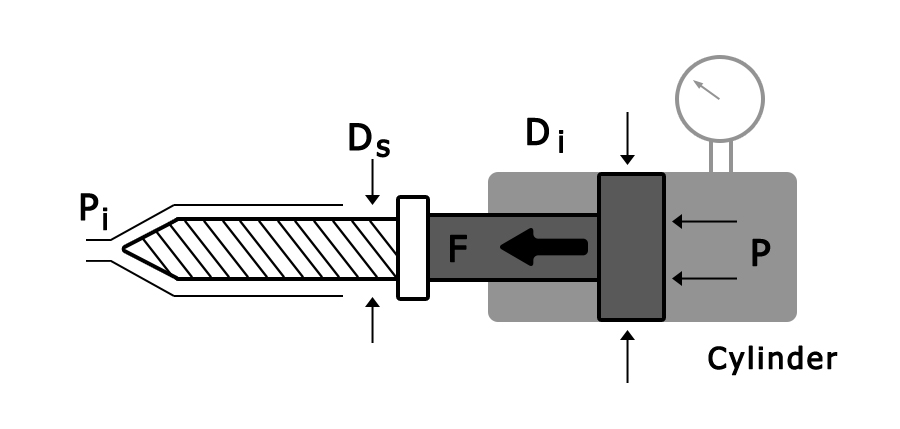
Presión de embalaje
La presión de empaque, también conocida como presión de mantenimiento o presión de segunda etapa, es una fase del proceso de moldeo por inyección donde se aplica presión adicional al material plástico fundido después de la inyección inicial en la cavidad del molde. Esta presión se mantiene durante un período específico durante la fase de empaque o retención del ciclo de moldeo. El propósito principal de la presión del empaque es compensar la contracción y asegurar el llenado completo del molde, contribuyendo a la producción de piezas moldeadas de alta calidad.[11]
Contrapresión
En el proceso de fundir y plastificar plásticos, el material fundido sigue moviéndose hacia el extremo frontal del cilindro (dentro de la cámara de medición) y cada vez más, formando gradualmente una presión que empuja el tornillo hacia atrás. Para evitar que el tornillo retroceda demasiado rápido y asegurar una compactación uniforme de la masa fundida, es necesario proporcionar una presión en la dirección opuesta a la del tornillo, y esta presión en la dirección opuesta para evitar que el tornillo retroceda es llamada contrapresión.[12]
Tornillo RPM
Las RPM del tornillo se miden en revoluciones por minuto, lo que indica cuántas veces el tornillo completa una rotación completa en un minuto.
Punto de conmutación V/P
El punto de conmutación V/P, también conocido como punto de conmutación de velocidad a presión, es un parámetro en el moldeo por inyección que se refiere al punto de transición durante el proceso de inyección cuando la máquina cambia del control de velocidad al control de presión. Esta transición es importante para optimizar el proceso de moldeo por inyección y lograr piezas moldeadas consistentes y de alta calidad.
Durante las primeras etapas del proceso de inyección, la máquina normalmente funciona en modo de control de velocidad. En este modo, la velocidad de inyección es el principal parámetro controlado. A medida que el molde se llena y el material se solidifica, la máquina cambia al modo de control de presión, donde la presión de inyección se convierte en el principal parámetro controlado.
El punto de conmutación V/P es el punto del ciclo de inyección en el que la máquina pasa del control de velocidad al control de presión. Esta transición es crucial para evitar problemas como el embalaje excesivo o insuficiente del molde, que puede afectar la calidad de las piezas moldeadas.
Chupar de nuevo
"Succionar hacia atrás" en el contexto del moldeo por inyección se refiere a una retracción o movimiento hacia atrás deliberado del tornillo durante el ciclo de moldeo. Esto se hace para reducir o eliminar la presencia de material plástico fundido en el extremo del tornillo durante las fases de enfriamiento y solidificación del proceso de moldeo por inyección.
El objetivo principal de implementar la succión hacia atrás es evitar que el material fundido gotee o se forme después de que se haya llenado el molde y antes de que el molde se abra para expulsar la pieza. El babeo ocurre cuando queda un exceso de material en la boquilla o en el sistema de canal, lo que lleva a la formación de gotas o hilos de plástico no deseados.
Así es como suele funcionar la succión:
- Una vez lleno el molde, el tornillo se retrae o retrocede brevemente.
- Este movimiento hacia atrás crea un vacío o una presión negativa en la parte delantera del tornillo.
- La presión negativa hace que cualquier exceso de material plástico fundido en la boquilla o en el sistema de canal regrese al barril.
T4. Luego, el molde pasa por las fases de enfriamiento y solidificación sin riesgo de babear o formar hilos.
La succión es especialmente útil cuando se trabaja con termoplásticos que tienen tendencia a formar hilos o babear, y ayuda a producir piezas moldeadas más limpias y precisas. La cantidad de succión suele ser ajustable y el ajuste óptimo depende de factores como el material que se utiliza y los requisitos específicos de la aplicación de moldeo.
Amortiguar
En el moldeo por inyección, el término "cojín" se refiere a la pequeña cantidad de material plástico fundido que se deja intencionalmente en el cilindro al final de la carrera de inyección. Este cojín de material cumple varios propósitos importantes en el proceso de moldeo:
- Compensación de la contracción: a medida que el material plástico se enfría y solidifica dentro del molde, sufre una contracción. El cojín compensa esta contracción proporcionando material adicional que puede fluir hacia el molde para llenar los huecos creados por la solidificación del plástico.
- Prevención de disparos cortos: Un disparo corto ocurre cuando no hay material suficiente para llenar completamente la cavidad del molde. El cojín ayuda a evitar disparos cortos al garantizar que haya suficiente material en el cañón para compensar cualquier variación en el proceso de moldeado.
3.Evitar el chorro: El chorro es un defecto que puede ocurrir cuando el plástico fundido se inyecta en el molde a alta velocidad, lo que provoca que el material se corte y se cree un flujo similar a una corriente. El cojín ayuda a reducir la velocidad y la presión de inyección, minimizando el riesgo de chorros.
Hora de espera
En el moldeo por inyección, el "tiempo de espera" se refiere al período durante el cual el material plástico fundido se mantiene bajo presión en el molde después de la fase de inyección. El objetivo principal del tiempo de espera es garantizar que la pieza moldeada adopte completamente la forma de la cavidad del molde y que se minimicen los posibles problemas, como marcas de hundimiento o huecos.
Durante el tiempo de espera, se deja que el material plástico en el molde se enfríe y solidifique bajo presión, lo que ayuda a evitar que el material se encoja o se deforme antes de que la pieza esté completamente formada. Esta fase es crítica para lograr las dimensiones, el acabado superficial y las propiedades mecánicas deseadas de la pieza moldeada.
Los puntos clave sobre el tiempo de espera en el moldeo por inyección incluyen:
- Mantenimiento de presión: La presión aplicada al material plástico fundido se mantiene durante el tiempo de espera para contrarrestar la contracción que se produce a medida que el material se enfría y solidifica. Esto es particularmente importante para materiales con tasas de contracción más altas.
- Congelación de la puerta: el tiempo de espera permite que la puerta (el punto donde el plástico fundido ingresa a la cavidad del molde) se congele o solidifique. Esto ayuda a prevenir la apertura prematura del molde, reduciendo el riesgo de rebaba (exceso de material) y asegurando que la pieza esté completamente formada.
4.Enfriamiento del material: el tiempo de espera contribuye al enfriamiento general de la pieza moldeada. El tiempo de enfriamiento es un factor crítico para lograr piezas consistentes y de alta calidad.
Tiempo de enfriamiento
El tiempo de enfriamiento en el moldeo por inyección se refiere al tiempo durante el cual la pieza moldeada permanece dentro del molde cerrado para permitir que el plástico fundido se enfríe y solidifique. El tiempo de enfriamiento es una etapa crítica en el ciclo de moldeo por inyección e influye directamente en la calidad, dimensiones y propiedades de la pieza moldeada final.
Los puntos clave sobre el tiempo de enfriamiento en el moldeo por inyección incluyen:
- Solidificación del plástico: el objetivo principal del tiempo de enfriamiento es garantizar que el material plástico fundido se solidifique completamente dentro de la cavidad del molde. Este proceso es esencial para lograr la forma deseada y la integridad estructural de la pieza moldeada.
- Minimizar la deformación y la contracción: un enfriamiento adecuado es crucial para minimizar el riesgo de deformación y contracción de la pieza. El enfriamiento controlado y uniforme ayuda a prevenir la distribución desigual de tensiones dentro del material.
- Optimización del tiempo de ciclo: si bien los tiempos de enfriamiento más prolongados pueden contribuir a una mejor calidad de las piezas, los tiempos de ciclo más cortos generalmente son más deseables para maximizar la eficiencia de la producción. Es esencial equilibrar el tiempo de enfriamiento con otros factores, como el diseño de la pieza y las propiedades del material.
- Control de temperatura: la temperatura del molde juega un papel importante en el proceso de enfriamiento. Muchos moldes tienen canales de enfriamiento a través de los cuales circula un fluido con temperatura controlada (generalmente agua) para controlar la temperatura del molde y acelerar el proceso de enfriamiento.[13]
Fuerza de sujecion
La fuerza de sujeción es un parámetro crítico en el moldeo por inyección, refiriéndose a la fuerza aplicada al molde para mantenerlo cerrado durante las fases de inyección y enfriamiento del proceso de moldeo. La fuerza de sujeción es esencial para mantener la integridad de la pieza moldeada y evitar que el plástico se escape del molde.[14]
La fuerza de sujeción requerida depende de varios factores, incluido el material que se está moldeando, el tamaño y la forma de la pieza y la presión de inyección. No existe una fórmula universal para calcular la fuerza de sujeción porque está influenciada por varios factores y diferentes máquinas de moldeo por inyección pueden tener diferentes requisitos de fuerza de sujeción.
Sin embargo, un enfoque común para estimar la fuerza de sujeción es utilizar el área proyectada de la pieza moldeada y la presión de inyección. La fórmula es:
Fuerza de sujeción = Presión de inyección × Área proyectada de la pieza
Aquí, el área proyectada es el área máxima de la pieza vista desde la dirección de la abertura del molde. La presión de inyección es la presión necesaria para llenar el molde con plástico fundido.
Productos generales:
Fuerza (Ton) > Área proyectada del producto (㎠) × presión interna del molde de resina (kgf/㎠) × 10-3
Peso de disparo
El peso del granallado es un parámetro crítico en el moldeo por inyección y se refiere a la cantidad de material (generalmente en gramos u onzas) inyectado en el molde para producir una sola pieza moldeada. Es un factor clave en el proceso de moldeo, ya que afecta la calidad, dimensiones y propiedades del producto final.
El peso del disparo está determinado por la gravedad específica del material, la geometría de la pieza y las cavidades del molde. Es esencial controlar con precisión el peso de la granalla para garantizar una producción constante y de alta calidad. Un peso de inyección insuficiente o excesivo puede provocar defectos en las piezas moldeadas.
Para calcular el peso del disparo, puede utilizar la siguiente fórmula:
Peso del disparo = Gravedad específica del material × Volumen de la pieza
Aquí, la gravedad específica del material es la relación entre la densidad del material de moldeo y la densidad del agua, y el volumen de la pieza es el volumen de la pieza que se va a moldear. La gravedad específica se puede encontrar en las hojas de datos de materiales proporcionadas por los proveedores de materiales.
Es importante tener en cuenta que el peso del disparo puede verse influenciado por factores como el diseño del molde, la contracción del material y las capacidades de la máquina de moldeo por inyección. Las máquinas de moldeo por inyección generalmente se clasifican según su tamaño máximo de disparo, que representa la cantidad máxima de material que pueden inyectar en un solo disparo.
Capacidad de tiro
El término "capacidad de disparo" en el moldeo por inyección generalmente se refiere a la cantidad máxima de material que una máquina de moldeo por inyección puede inyectar en un solo disparo. Este es un parámetro crucial, ya que influye en el tamaño y la complejidad de las piezas que se pueden producir. La capacidad de inyección suele ser especificada por el fabricante de la máquina de moldeo por inyección.
La fórmula para la capacidad de disparo es:
Capacidad de disparo = Carrera máxima de inyección × Área de sección transversal del tornillo
Aquí:
Carrera máxima de inyección
La carrera máxima de inyección es la distancia máxima que puede recorrer el tornillo de inyección durante la fase de inyección. Por supuesto, incluirá cavidad, canal de bebedero y cojín, deberás calcularlo.
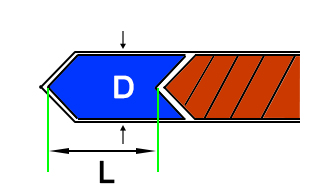
Área de la sección transversal del tornillo
El área de la sección transversal del tornillo es el área de la sección transversal del tornillo de inyección. Se calcula usando la fórmula para el área de un círculo (π×(Radio) 2 )/4, donde el radio es la mitad del diámetro del tornillo.
Es importante tener en cuenta que la capacidad de disparo está influenciada por factores como el diseño de la unidad de inyección, el tamaño del tornillo y las especificaciones generales de la máquina. La capacidad máxima de inyección suele estar indicada en las especificaciones técnicas de la máquina de moldeo por inyección.
Ciclo de inyección
El ciclo de moldeo por inyección se refiere a la secuencia completa de eventos y fases que ocurren durante la producción de una pieza moldeada utilizando una máquina de moldeo por inyección. El ciclo consta de varias etapas, cada una con sus tareas y propósitos específicos. Incluye principalmente abrazadera de molde, inyección, prensa de empaque, enfriamiento/alimentación y expulsión. Otros pasos que no son muy críticos no serán discutidos por el momento.
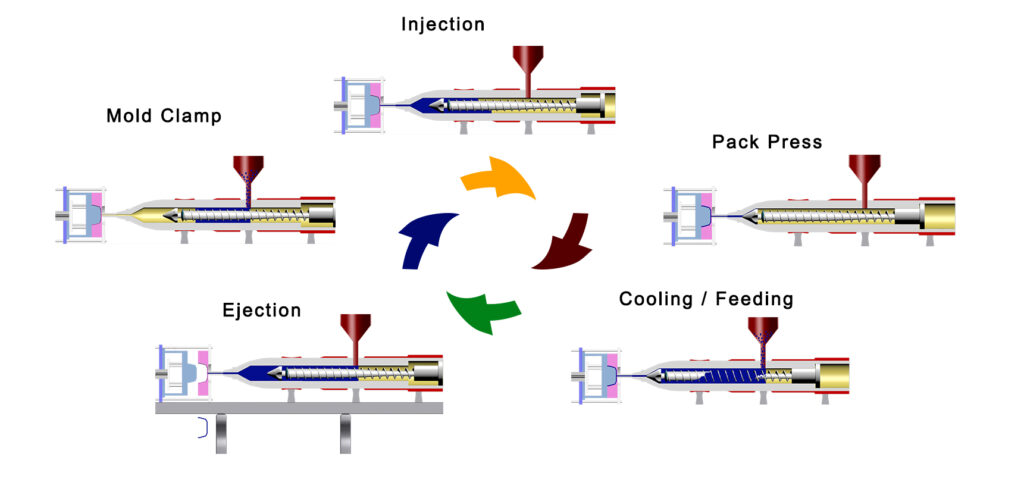
Aquí hay algunos términos más profesionales.
Cierre del molde
El “cierre del molde” es una de las etapas clave en el ciclo de moldeo por inyección. Se refiere al proceso de cerrar las dos mitades del molde (comúnmente conocido como “sujeción” del molde) antes de la inyección de material plástico fundido. El molde debe estar bien cerrado para soportar la presión del material inyectado y asegurar la formación precisa de la pieza moldeada.
La etapa de cierre del molde incluye los siguientes pasos:
- Alineación: Las dos mitades del molde, que están montadas en las placas móviles y estacionarias de la máquina de moldeo por inyección, están alineadas correctamente.
- Cierre: La placa móvil, a menudo unida a la mitad móvil del molde, se mueve hacia la placa estacionaria, juntando las dos mitades del molde. El molde se cierra de forma segura con la ayuda de una unidad de cierre.
En la producción real, la razón por la que se requiere un movimiento a baja velocidad en el momento en que finalmente se cierra el molde es por la preocupación por el daño del molde causado por un desmolde deficiente o por rebabas del producto moldeado.
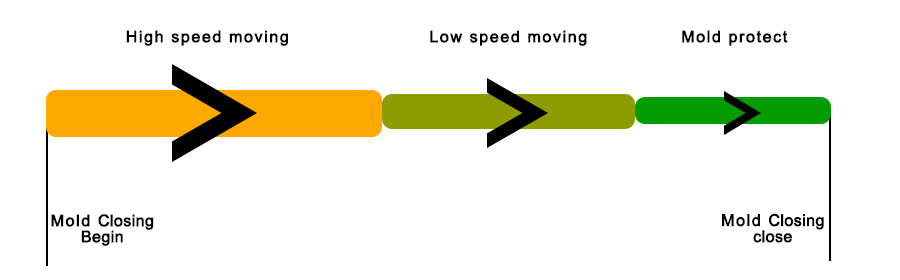
Sujeción del molde
La sujeción del molde es una etapa crítica en el proceso de moldeo por inyección que implica cerrar y sujetar de forma segura las dos mitades del molde, conocidas como la mitad estacionaria (platina fija) y la mitad móvil (platina móvil o ariete), para crear una cavidad sellada para la inyección de material plástico fundido. [15]
El proceso de sujeción es esencial para mantener la integridad estructural del molde y evitar el escape de material fundido durante la inyección.
Avance de la boquilla
Una vez cerrado el tipo, soporta la fuerza del molde para evitar que el molde sea empujado por la presión de la resina que fluye que permite que se produzca la boquilla durante el moldeo por inyección.
Plastificación
Cuando la resina en el molde se cura, la etapa de fusión de la resina comienza dentro de la máquina de moldeo por inyección en preparación para el siguiente ciclo de inyección. (incluida la etapa de medición)
El material plástico se transporta a través de una garganta de alimentación hasta el cilindro calentado de la máquina. Dentro del cañón hay un tornillo giratorio que sirve para varios propósitos. El calor generado por el cilindro y la energía mecánica del tornillo giratorio trabajan juntos para derretir el material plástico. El proceso de fusión convierte los gránulos de plástico sólidos en un estado fundido.
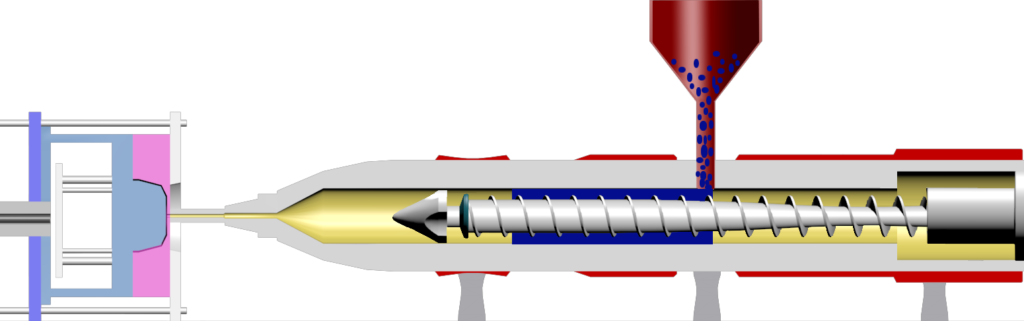
Inyección
Después de combinar la boquilla y el casquillo del bebedero, el tornillo de inyección avanza para suministrar resina fundida al molde.
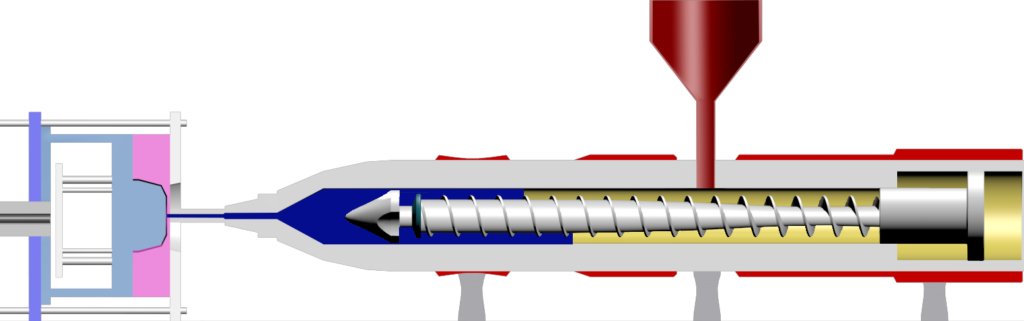
Tenencia
Mantener la presión, en el contexto de moldeo por inyección, se refiere a la presión que se mantiene sobre el material plástico fundido en la cavidad del molde después de la fase de inyección y antes de que se abra el molde. Esta fase se conoce comúnmente como fase de tenencia o de residencia. La presión de mantenimiento es un parámetro crítico en el proceso de moldeo por inyección y sirve para varios propósitos importantes: compensar la contracción, prevenir marcas de hundimiento y prevenir la congelación de la puerta.
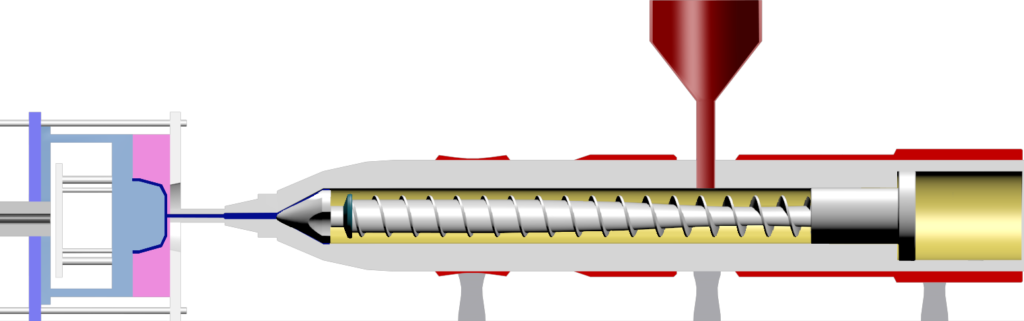
Enfriamiento
En el contexto del moldeo por inyección, "enfriamiento" se refiere a la etapa del ciclo de moldeo en la que se deja enfriar y solidificar el material plástico fundido, que se ha inyectado en la cavidad del molde y ha tomado la forma de la pieza deseada. El enfriamiento es un paso crucial en el proceso general de moldeo por inyección e influye significativamente en la calidad, las dimensiones y las propiedades mecánicas de la pieza moldeada final.
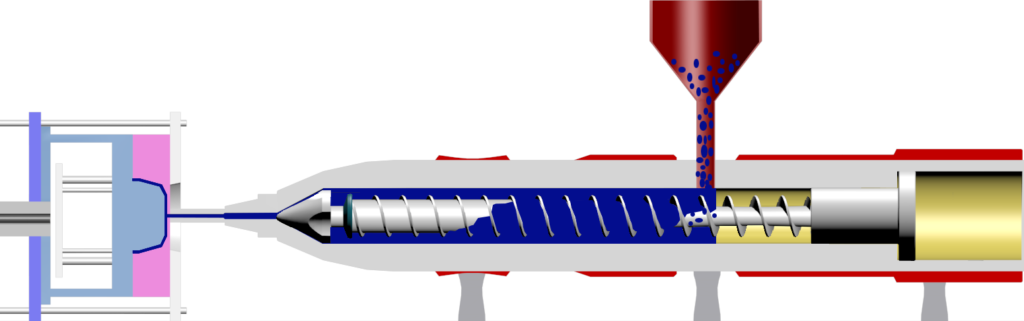
Retiro de la boquilla
Durante el proceso de enfriamiento de la resina moldeada, para evitar que la boquilla en la resina se solidifique debido al enfriamiento del molde. La boquilla retrocederá, liberará el contacto entre la boquilla y el casquillo del bebedero y se preparará para la siguiente etapa de moldeo por inyección. (Puede omitirlo si no le preocupa la solidificación de la boquilla)
Tiene funciones diferentes al avance de boquilla.
La sincronización y el movimiento específicos del retroceso de la boquilla se pueden programar y controlar para optimizar el proceso de moldeo por inyección para los requisitos específicos del material y la pieza que se están produciendo. Las máquinas de moldeo por inyección avanzadas suelen tener características que permiten un control preciso del movimiento de la boquilla y otros parámetros, lo que contribuye a la producción de piezas moldeadas de alta calidad.
Apertura y expulsión del molde
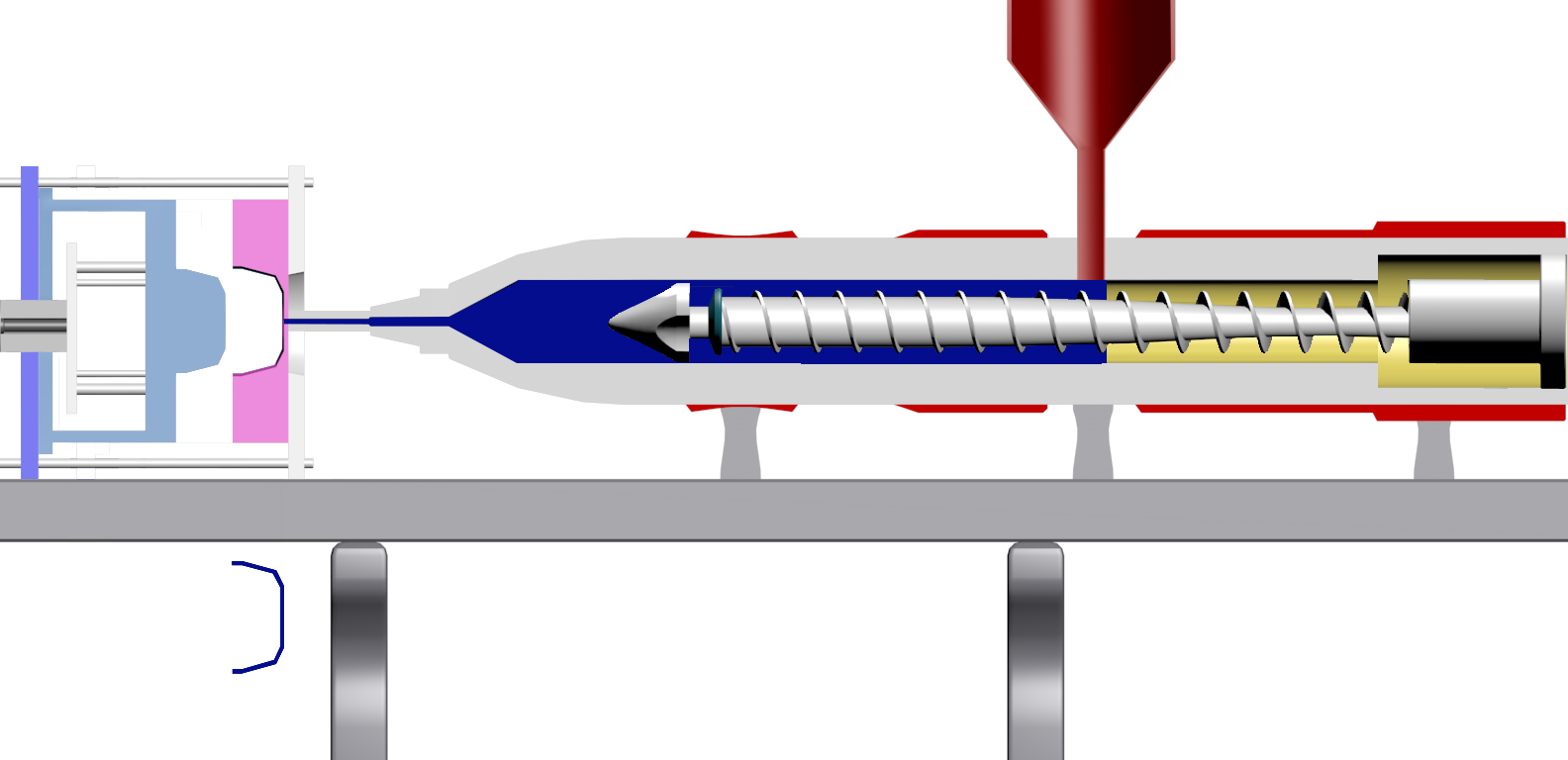
Una vez curada la resina y abierto el molde, el pasador eyector del lado fijo se mueve para expulsar el producto del molde.
Puntos clave sobre la etapa de expulsión en moldeo por inyección incluyen pasadores expulsores, sistema eyector, consideraciones de diseño de piezas, optimización del tiempo de ciclo y manejo de piezas.
Puntos clave de las condiciones del moldeo por inyección.
Conceptos básicos para establecer las condiciones iniciales de moldeo.
1) Temperatura: Ajuste lo más bajo posible (con el fin de evitar la descomposición y acortar el tiempo del ciclo)
2) Presión: La presión de inyección, la presión de compensación y la contrapresión están configuradas en nivel bajo (para evitar daños al molde causados por el exceso de embalaje).
3) Presión de embalaje: Mantenga el ajuste alto (para evitar rebabas y la seguridad del equipo)
4) velocidad
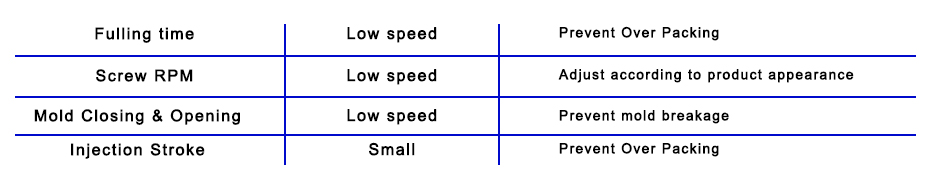
5) Horario
Cuando el material se enfría, se necesita mucho tiempo, especialmente durante la etapa de mantenimiento de la presión, para garantizar que la compuerta esté sellada.
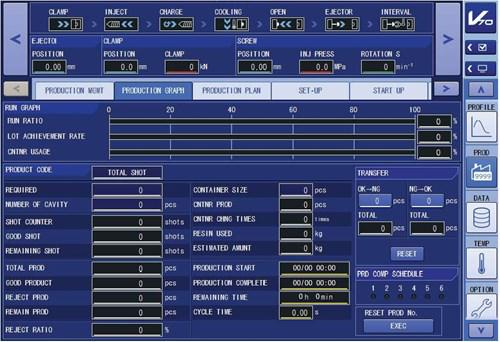
Moldeo por inyección en etapas (moldeo por inyección en varias etapas)
Principio:
- Inyecte el pegamento a baja velocidad para la primera inyección, mueva la boquilla al cabezal frío y luego aumente la segunda velocidad de inyección para llenar la cavidad del molde y acortar el tiempo que tarda el plástico en fluir hasta el final de la compuerta, de modo que que la viscosidad del plástico durante el llenado se pueda mantener al mínimo y solidificarse. Sin embargo, es difícil controlar el punto de conmutación de mantenimiento de presión correcto para la inyección de alta velocidad, por lo que se debe utilizar una desaceleración de múltiples etapas para controlar eficazmente el punto de conmutación de mantenimiento de presión.
- El principio de acción de la inyección segmentada: el control electroóptico se utiliza para ordenar a la válvula proporcional de flujo en el sistema hidráulico obtener instantáneamente la velocidad de inyección en un punto para lograr la velocidad de inyección segmentada.
Método de ajuste de velocidad de moldeo por inyección:
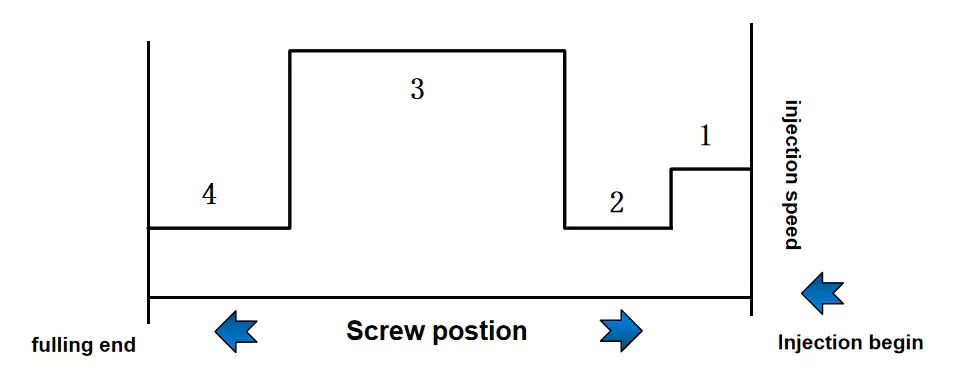
1) Sección del canal de bebedero: alta velocidad en la etapa inicial a velocidad media en la producción en masa (para evitar la solidificación y el sobrecalentamiento).
2) Entrada de pegamento: baja velocidad (evita Jetting, Silver Streak, etc.).
3) Sección de moldeo: Alta velocidad (Prevención de Marcas de Flujo, Soldadura).
4) Parte de mantenimiento de presión: baja velocidad (se reducen el gas, las rebabas, etc. y la posición de conmutación de la presión de mantenimiento es importante).
Función de velocidad de moldeo por inyección
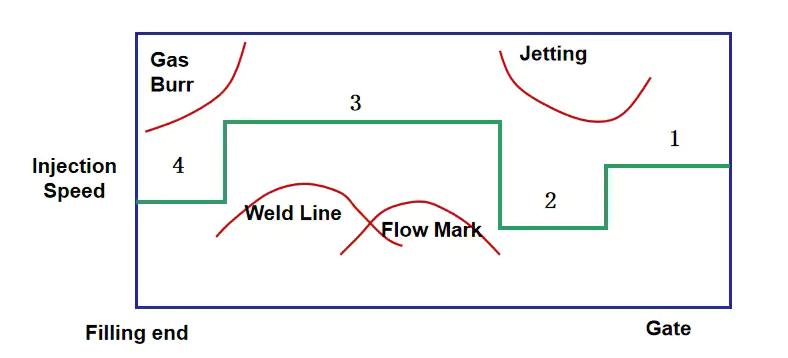
1) Para evitar Jetting o Silver Streak alrededor de la puerta, es necesario hacerlo a baja velocidad.
2) Para evitar marcas de flujo o líneas de soldadura, se requiere alta velocidad.
3) Para evitar quemaduras o rebabas de gas, se requieren velocidades medias y bajas y un cambio seguro.
Estado de espera
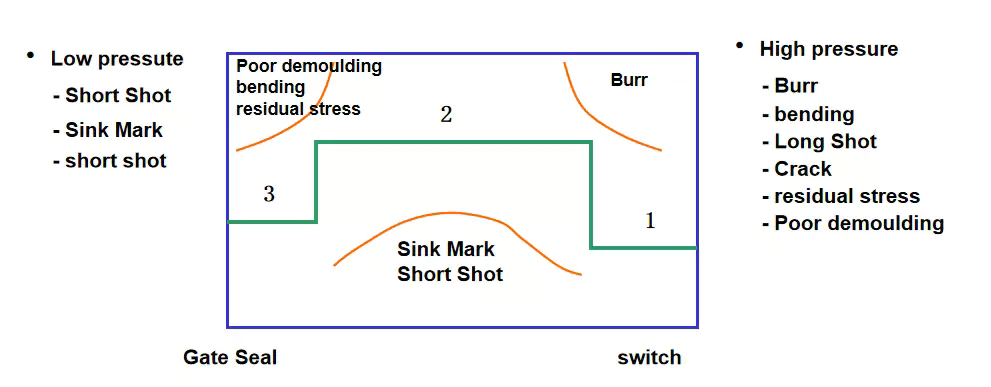
1) Para evitar rebabas, utilice baja presión.
2) Para evitar que la marca de hundimiento o el número establecido se reduzcan, se requiere alto voltaje
3) Para evitar tensiones residuales, se requiere baja presión.
Distribución de presión dentro del molde durante el proceso de moldeo por inyección.
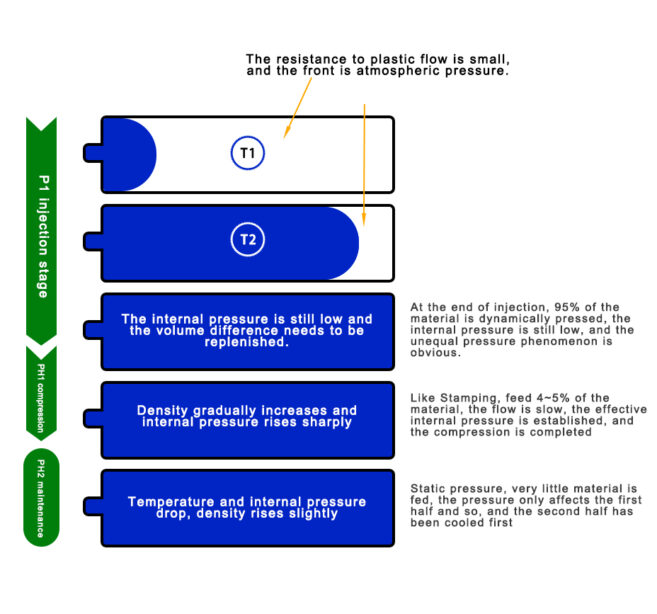
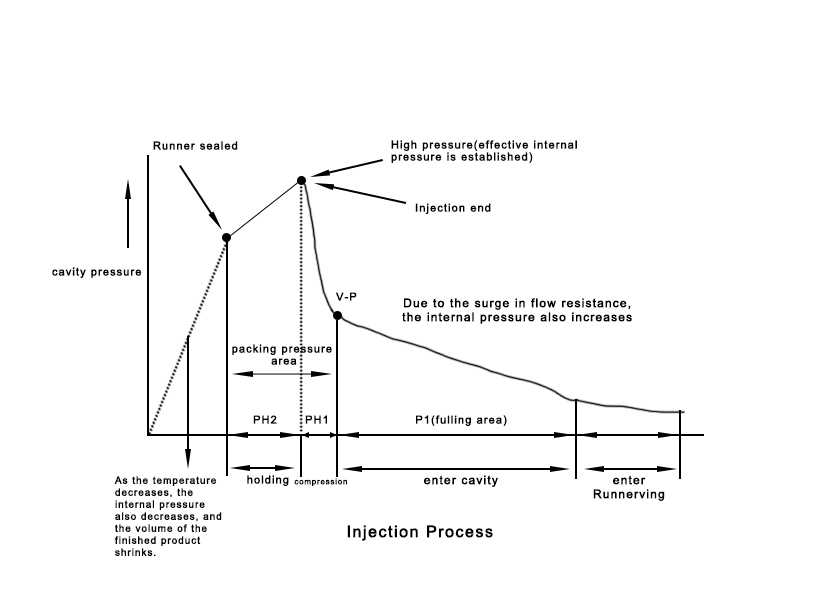
Cambios de presión dentro de la cavidad cuando se cambia V/P
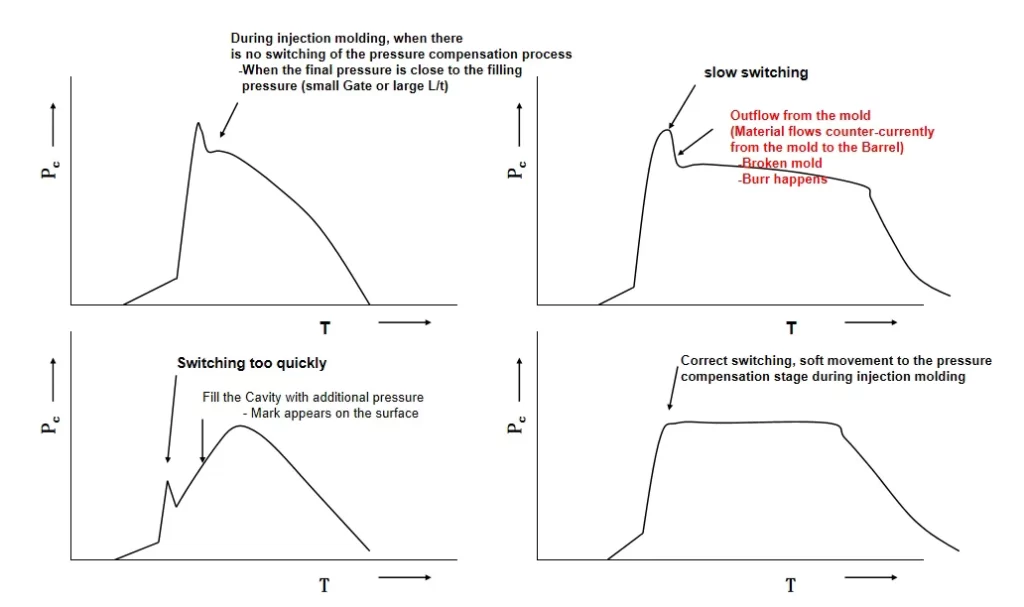
Efecto de las condiciones del moldeo por inyección sobre la tasa de contracción.
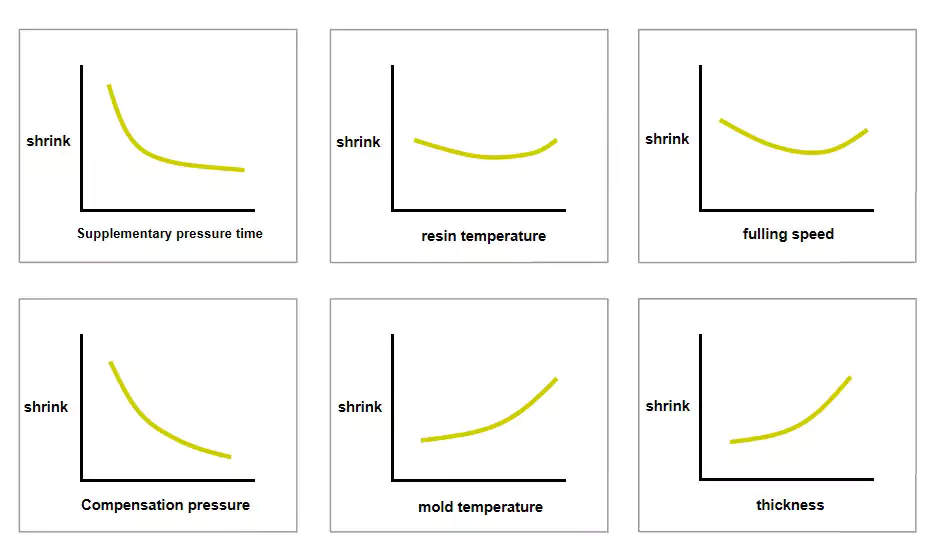
Optimización del proceso de moldeo por inyección:
Mediante las condiciones de fraguado inicial del moldeo por inyección, se acorta el tiempo de fraguado y el número de pruebas del molde.
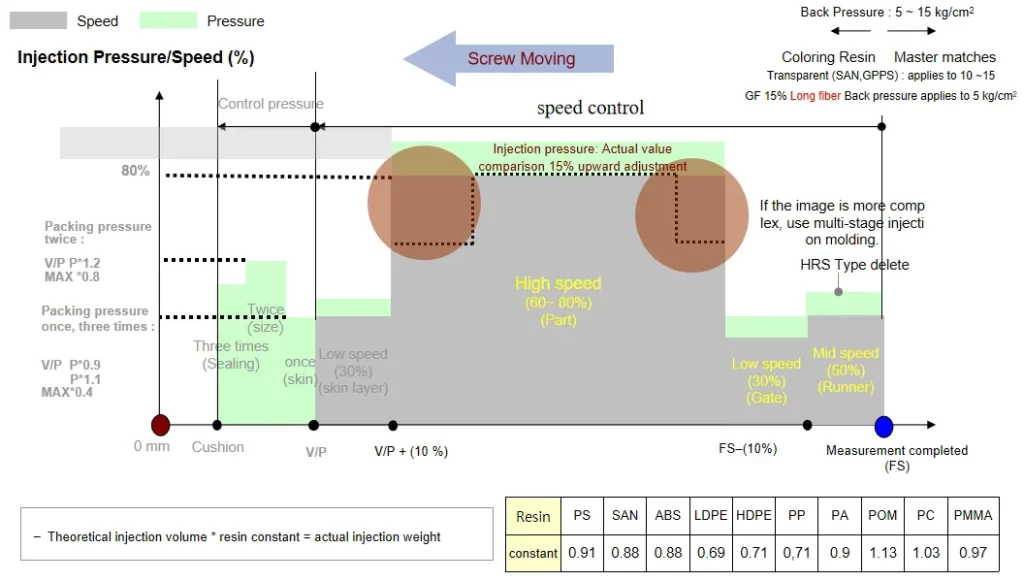
Referencias:
- [1] Z. Tadmor, Orientación molecular en moldeo por inyección, J. Appl. Polimero. Ciencia. 18 (6), págs. 1753–1772, 1974. doi:10.1002/app.1974.07018061
- [2] M. Huszar et al. La influencia del flujo y las propiedades térmicas en la presión de inyección y la predicción del tiempo de enfriamiento App Math Model (2016)
- [3] PC Roozemond et al. Modelado de la cristalización inducida por flujo en polipropileno isotáctico a altas velocidades de corte J Rheol (NYNY) (2015)
- [4] O. Ogorodnyk y otros. Monitoreo y control del moldeo por inyección de termoplásticos una revisión Procedia CIRP (2018)
- [5] Análisis de presión del moldeo por inyección dinámico y optimización de parámetros de proceso para reducir la deformación de productos moldeados por inyección Xinyu Wang, Hongxia Li, Junfeng Gu,2 Zheng Li, * Shilun Ruan, Changyu Shen y Minjie Wang
- [6] Optimice los parámetros del proceso de moldeo por inyección y cree un sistema de control de proceso adaptativo basado en el perfil de presión de la boquilla y la fuerza de sujeción. Guan-Yan Liou, Wei-Jie Su, Feng-Jung Cheng, Chen-Hsiang Chang, Ren-Ho Tseng, Sheng-Jye Hwang, * Hsin-Shu Peng y Hsiao-Yeh Chu https://www.ncbi.nlm .nih.gov/pmc/articles/PMC9921389/
- [7] Optimización rápida del perfil de velocidad de inyección basada en la teoría de grafos. Peng Zhao, Ding Yang, Huamin Zhou y Kai Xu
- [8] Huang, MS Predicción gris basada en la presión de la cavidad del punto de cambio de llenado a empaque para moldeo por inyección. J. Mater. Proceso. Tecnología. 2007, 183, 419–424.
- [9] Huang, MS; Nian, Carolina del Sur; Chen, JY; Lin, CY Influencia de la fuerza de sujeción en el alargamiento de la barra de unión, la separación del molde y las dimensiones de las piezas en el moldeo por inyección. Resumen. Ing. 2018, 51, 647–658.
- [10] Manual de moldeo por inyección Dominick V. Rosato PE, Donald V. Rosato PH.D. & Marlene G. Rosato PE
- [11] Libro de estrategias, objetivos, técnicas y herramientas de gestión de la energía en el procesamiento de plásticos • Tercera edición • 2019
- [12] XIONG Wen nan, ZHANG Ya jun, JIN Zhi ming et al., “Investigación sobre el consumo de energía del proceso de sujeción de una máquina de moldeo por inyección basada en AMESim [J]”, Plásticos, vol. 47, núm. 5, págs. 122-125, 2018.
- [13Método científico para determinar el tiempo de enfriamiento en moldeo por inyección mediante termografía infrarroja autor: Boud, Eric D
- [14] https://zeus.plmsc.psu.edu/~manias/MatSE447/17-22_Processing.pdf
- [15] ¿Qué es la fuerza de sujeción en el moldeo por inyección? FUTEK https://www.futek.com/applications/Injection-Molding-Force-Feedback
Guía básica para el procesamiento de moldeo por inyección by capaz de mecanizar está licenciado bajo CC BY-NC 4.0