Urethane Casting
Urethane casting is a method used to create high-quality plastic parts, prototypes, and models. It is a cost-effective and efficient way to produce small batches of parts that are identical to the original design.
The urethane casting process involves pouring liquid polyurethane into a silicone mold. The mold is created from a master pattern, which can be made from a 3D printed model, a CNC machined part, or even a hand-carved sculpture. Once the mold is filled, the polyurethane is left to cure and harden. When the part is removed from the mold, it is trimmed and finished to meet the desired specifications.

The Urethane Casting: Step by Step
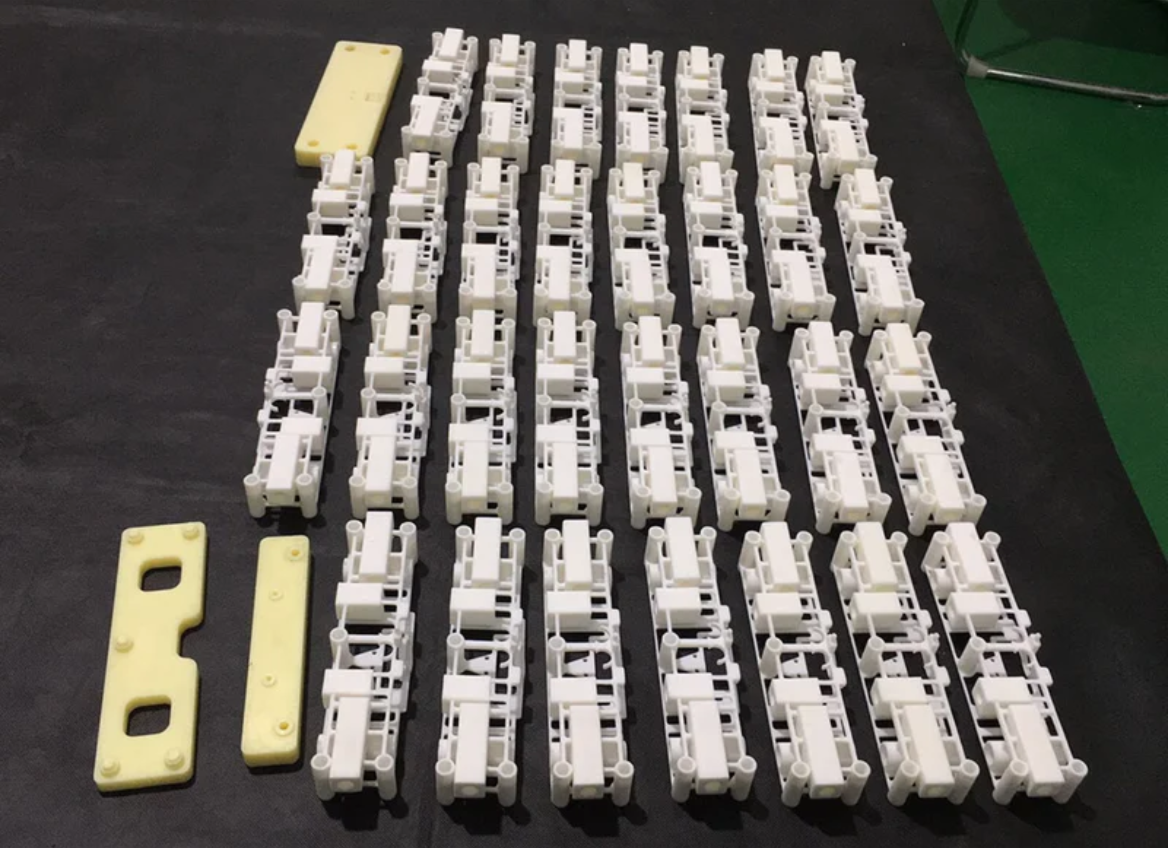
The urethane casting can produce part with character very like some thermoplastics, for example ABS, PC and more. Take ABS as an example. To create an ABS-like material using urethane casting, often a two-part polyurethane system is used. This system typically includes a base material and a hardener or curing agent. In order to simulate the properties of ABS thermoplastic, the base material may include additives such as fillers, pigments, or other chemicals that modify the material’s physical properties, including its rigidity, flexibility, and impact resistance. By adjusting the composition of the base material and the hardener, it’s possible to closely replicate the properties of ABS thermoplastic and achieve an ABS-like material using urethane casting.
Advantages of Urethane Casting
Cost-effective
Urethane casting is generally more cost-effective than other manufacturing processes like injection molding, especially for small to medium production runs. It requires less expensive tooling, setup, and production equipment.
Versatility
Urethane casting can be used to create parts with a wide range of shapes, sizes, and textures, and can also simulate the properties of different materials such as ABS, polycarbonate, or silicone.
Rapid prototyping
With urethane casting, you can quickly produce prototype parts for testing and evaluation, allowing you to refine and improve your design before committing to more expensive production methods.
High-quality surface finish
Urethane cast parts usually have a smooth and consistent surface finish, making them ideal for end-use parts, visual models, and display pieces.
Wide selection of materials
There are many different types of urethane materials to choose from, each with unique mechanical, thermal, and chemical properties. This allows you to select the right material for the specific application.
Low-risk production
Since the tooling and equipment costs are lower, there’s less risk involved in producing small to medium production runs, which can be especially beneficial for start-ups or new product launches.
CapableMachining Vacuum Casting Materials
Material | Color | Temperature resistance | Paintable | Feature |
---|---|---|---|---|
ABS-like | Naturally white and multi colors are available as required. | 40-50℃ | Y | Good Hardness |
Nylon-like | White | Y | Resilient | |
Nylon GF-like | Black | 120℃ | Y | Good Strength |
PC-like | translucent/transparent | 40-50℃ | Y | Resilient |
POM-like | Naturally white and multi colors are available as required. | 40-50℃ | Y | Good Hardness |
TPU-like | Color can be adjusted as required | 100℃ | Y | Shore Hardness40-90 |
Silicone Rubber-like | Color can be adjusted as required | 100℃ | Y | Shore Hardness40-90 |
Take your product ideas to the next level with CapableMachining’s urethane casting service!
Our team of experts specializes in producing high-quality plastic parts and prototypes using state-of-the-art equipment and cutting-edge techniques. We offer a wide selection of urethane materials to choose from, each with unique properties to match your specific application. And with our quick turnaround times, low tooling costs, and ability to produce small to medium production runs, you can bring your products to market faster and more cost-effectively than ever before. Don’t settle for less – click the button below for all your urethane casting needs!