High pressure Die casting in Illinois
High pressure Die casting for Illinois
Welcome to our Die Casting Service, where precision meets efficiency, crafting quality components for your industry needs.
Custom Parts, On Demand Manufacturing
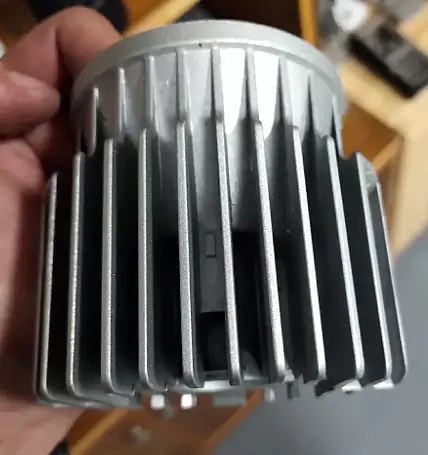
We Provide Satisfactory High pressure Die casting services in Illinois
Provide you with high-quality and cost-effective cast parts.
Welcome to Capable Machining, your premier destination for top-quality die casting services. With years of experience and expertise in the industry, we specialize in providing precision die casting solutions for a wide range of industries. Our state-of-the-art equipment and skilled team ensure that we can meet the most demanding specifications and deliver exceptional results every time. Whether you need prototype development or high-volume production, we have the capabilities to meet your die casting needs efficiently and effectively. Choose Capable Machining for reliable and cost-effective die casting services that meet and exceed your expectations.
Type services
We offer versatile die-casting services tailored to your product specifications, utilizing both hot chamber and cold chamber systems. Hot chamber systems cater to alloys like zinc, tin, and lead with lower melting points, while cold chamber die-casting machines excel with high melting temperature alloys such as aluminum, brass, and magnesium. Ensuring top-tier manufacturing solutions for your diverse needs.
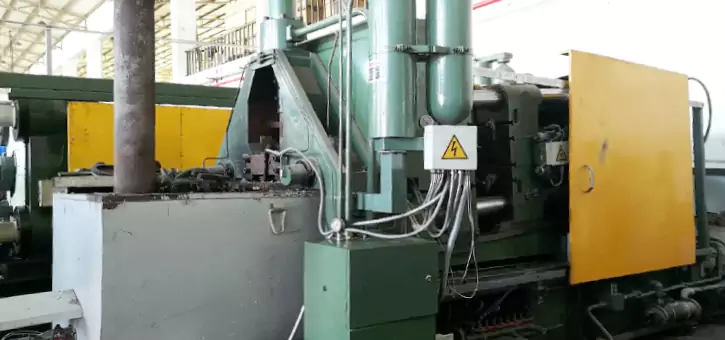
Hot chamber system
Hot chamber die-casting machines are used for alloys with lower melting points. The molten metal flows into the injection chamber through the inlet, and the hydraulically driven plunger forces the molten metal through the gooseneck channel and into the mold.

Cold chamber system
Cold chamber die-casting machines are used for alloys with high melting temperatures. The molten metal is still kept in an open insulated tank. These alloys cannot be cast in hot chamber die-casting machines because they will damage the pumping system.
Relative services
Capabilities
Equipment
Hot chamber system: clamp force up to 400 tons
Cold chamber system: clamp force up to 800 tons
Tolerances
Product: Heavily depending on the part type and the size of the part, typically +/- 0.1mm or +/-0.04 inch
Tooling tolerance: typically +/- 0.01mm or +/-0.004inch
Mold Life Cycle
Typically 30,000~50,000
Leading Time
Tooling: 35 days
Casting: 5~7 days
Material
Aluminum Alloy: ADC7,ADC10, ADC12,ADC14 A380, A360, A353
Zinc Alloy: ZA,ZA12, ZA27, AG-40, AG-41
Magnesium Alloy: AZ91D, AZ80M, AZ31B, AM60B, M2M
Thin wall
Typical: >1.5mm(depend on parts type and size)
Common Materials
Die casting materials are divided into the following three categories according to the properties of the metal materials used
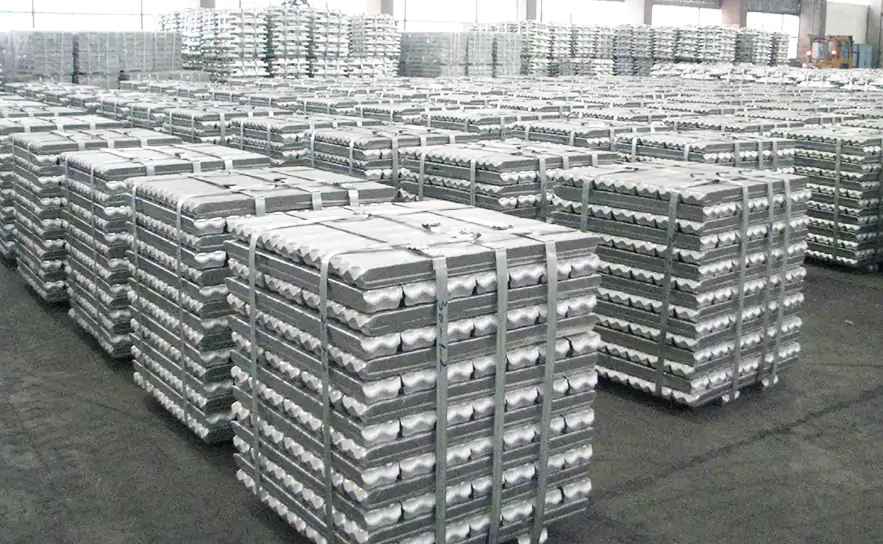
Aluminum alloys
Die-casting aluminum alloys have good performance and process performance, so the die-casting of aluminum alloys has developed rapidly and has been widely used in various industrial sectors.
Material properties:
- Strong and durable: Aluminum alloys are tough, hard, and resist corrosion. For instance, parts made from ADC12 are both sturdy and wear-resistant.
- Efficient heat transfer: Aluminum alloys boast exceptional thermal conductivity. This efficiently spreads and dissipates heat, enhancing parts’ ability to withstand high temperatures. This is particularly crucial in applications like car engines, electric fans, and LED lights, where efficient heat dissipation is essential.
- Easy to mold: Aluminum alloys are highly fluid, allowing them to effortlessly fill molds and solidify rapidly to create desired parts. This ease of molding enables efficient mass production of numerous identical or diverse parts within a short timeframe.
common types: ADC7,ADC10, ADC12,ADC14 A380, A360, A353
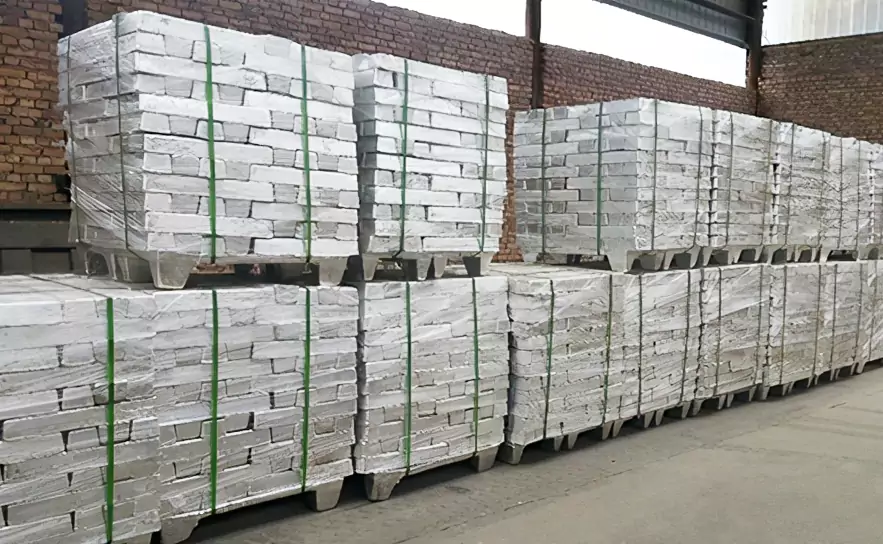
Magnesium alloys
Magnesium alloy is an alloy composed of magnesium and other elements. The main alloying elements are aluminum, zinc, manganese, cerium, thorium and a small amount of zirconium or cadmium.
Material properties:
- Light weight, high specific stiffness, high specific strength, strong thermal conductivity
- Good machining performance, good impact resistance and compression resistance
- Good die-casting performance, good dimensional accuracy and stability
- Good regeneration, can be completely recycled
- Low corrosion resistance, flammable and explosive
Mainly used in aerospace, military, automobile, motorcycle and 3C electronic products.
Type: AZ91D, AZ80M, AZ31B, AM60B, M2M
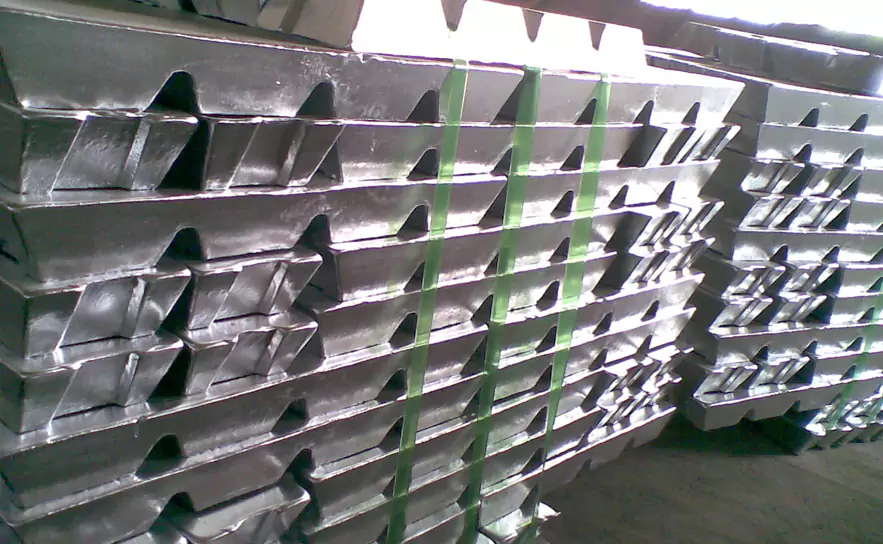
Zinc alloys
Zinc alloy is an alloy composed of zinc and other elements. Often added alloying elements are aluminum, copper, magnesium, cadmium, lead, titanium and other low-temperature zinc alloys.
Material properties:
- Large specific weight; good casting performance, can die-cast precision parts with complex shapes and thin walls, and the surface of the castings is smooth;
- Surface treatment can be carried out: electroplating, spraying, painting, electrophoresis, polishing, water transfer printing, etc.;
- It has good mechanical properties and wear resistance at room temperature;
- Poor corrosion resistance, not suitable for use in high temperature and low temperature (below 0°C) working environment
Mainly used in toys, lamps, decorations, auto parts, mechanical and electrical parts, electrical components and their casings.
Type: AZ91D, AZ80M, AZ31B, AM60B, M2M, etc.
Our Quality Control
CapableMachining boasts a ingrained quality assurance framework and a team of capable technical engineers who diligently oversee every aspect of our product manufacturing process – from procuring excellent raw components to delivering impeccable finished goods that encompass metals and plastics. To sustain our devotion to superiority, we extensively utilize state-of-the-art testing technology and cutting-edge equipment to meticulously evaluate crucial parameters such as workpiece dimensions, hardness, tensile strength, and elongation at every stage of production. We seek to maintain utmost control over these data points to meet and surpass the expectations of our esteemed clientele consistently.
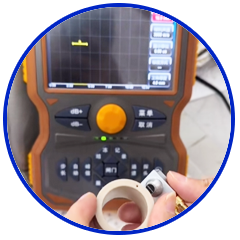
Professional quality control Engineer
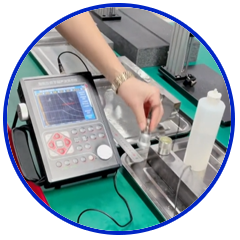
Tolerances up to ±0.0004″ (0.01mm)
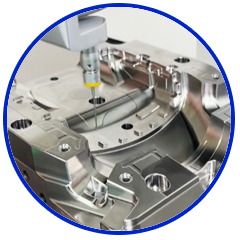
State-of-the-art Inspection Facilities
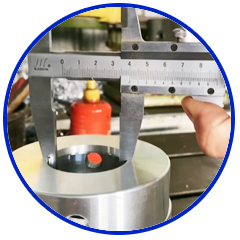
Proven and reliable quality control system.
Gallery of Parts
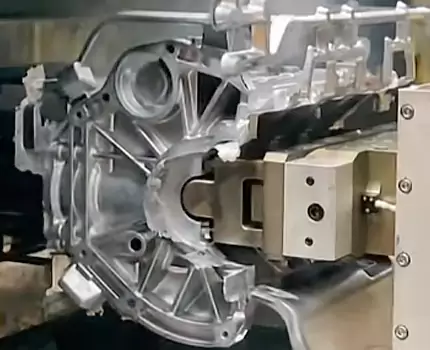
Auto Parts
Material: AL
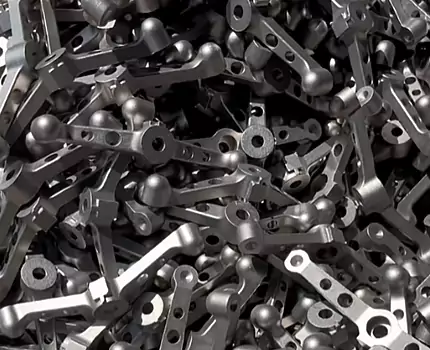
Equipment part
Material: AL
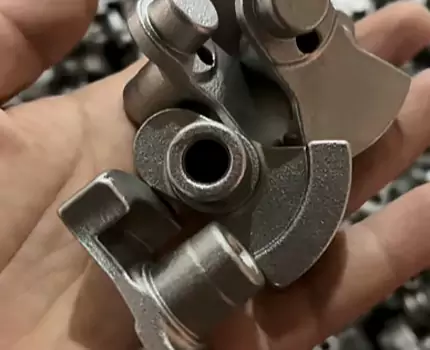
Comsumer part
Material: AL
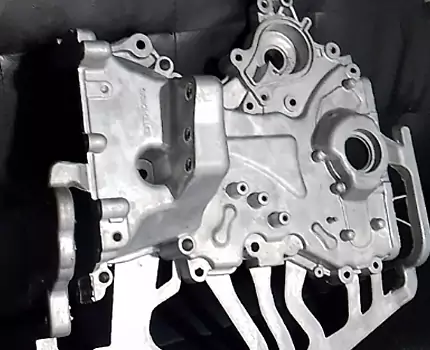
New energy auto
Material: AL
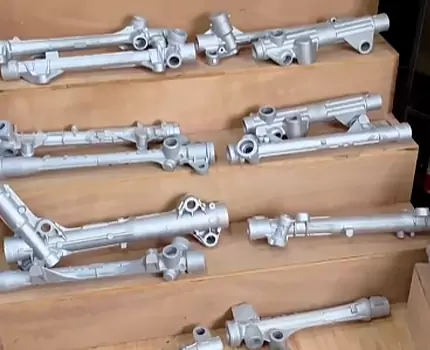
Industry parts
Material: AL
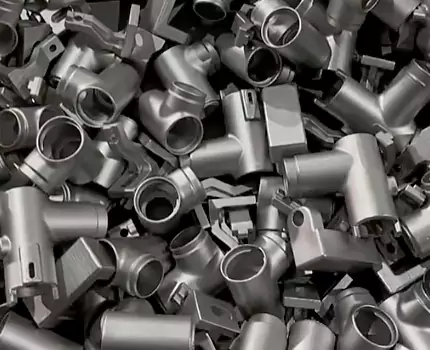
Agriculture machine parts
Material: AL
Other capabilities
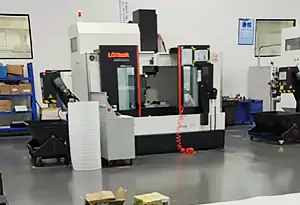
- Free & Automatic DFM feedback
- Tolerances: typically +/- 0.15mm or +/-0.006 inch
- Tooling: 30 days
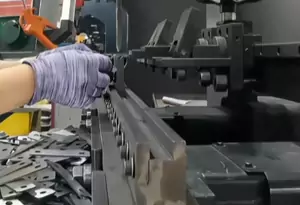
- Free advices from high trained engineers.
- Quotation in a few hours.leading time 3 days
- Fast delivery time
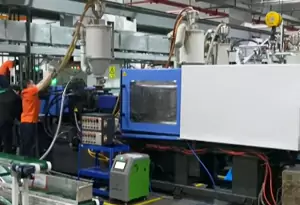
- Tolerances: typically +/- 0.15mm or +/-0.006 inch
- Free consultant ,Free DFM feedback
- Typically Tooling: 30 days
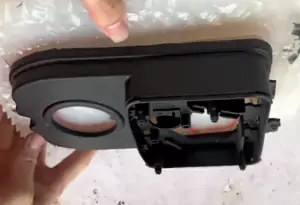
- Wide range of material choices
- Free consultant from engineers
- Fastest leading time: 1 day
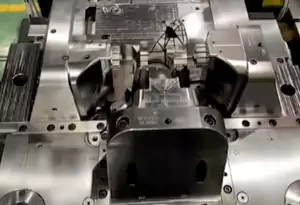
- Free & Automatic DFM feedback
- Tolerances up to ±0.00078″ (0.02mm)
- Rapid tooling: 7~12 days
How do find our location?
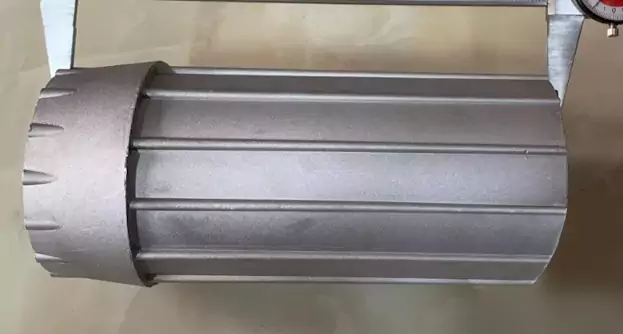
High pressure Die casting in Illinois
Other Location Near me
FAQ
Common Q&A about High Pressure Die Casting in Illinois
As a leading manufacturing process in Illinois, high pressure die casting offers a wide range of benefits for businesses looking to produce intricate and high-quality parts. To help you understand this process better, here are 10 common questions and answers:
Q: What is high pressure die casting?
A: High pressure die casting is a manufacturing process where molten metal is injected into a steel mold at high pressure to create complex shapes with precision.
Q: What materials can be used in high pressure die casting?
A: Various materials can be used in high pressure die casting, including aluminum, zinc, and magnesium.
Q: What are the advantages of high pressure die casting?
A: Some advantages of high pressure die casting include high productivity, dimensional accuracy, and the ability to create complex shapes with thin walls.
Q: How does high pressure die casting compare to other casting processes?
A: High pressure die casting is known for its high production rates, faster cycle times, and cost-effectiveness compared to other casting processes.
Q: Is high pressure die casting suitable for mass production?
A: Yes, high pressure die casting is ideal for mass production of parts due to its high efficiency and repeatability.
Q: What industries commonly use high pressure die casting in Illinois?
A: Industries such as automotive, aerospace, and electronics often utilize high pressure die casting for producing parts with complex geometries.
Q: How can a company in Illinois benefit from high pressure die casting?
A: By using high pressure die casting, companies in Illinois can achieve cost savings, shorter lead times, and high-quality products that meet strict specifications.
Q: What factors should a company consider when choosing a high pressure die casting provider in Illinois?
A: Companies should consider the provider’s experience, capabilities, quality assurance measures, and track record when selecting a high pressure die casting partner in Illinois.
Q: Are there any environmental considerations associated with high pressure die casting in Illinois?
A: High pressure die casting in Illinois can be environmentally friendly when proper waste management and recycling practices are implemented to minimize the impact on the environment.
Q: How can a company in Illinois get started with high pressure die casting?
A: To get started with high pressure die casting in Illinois, companies can reach out to experienced providers who can guide them through the process from design to production.
Conclusion
High pressure die casting is a versatile and efficient manufacturing process that offers numerous benefits for companies in Illinois looking to produce high-quality parts. By understanding the basics of high pressure die casting and partnering with experienced providers, businesses can take advantage of this innovative process to meet their production needs effectively.