Laser treatment of injection mold surfaces
Injection processing cannot be separated from the support of the injection mold, which makes up a large proportion of the entire mold industry.
An injection mold is a critical tooling component in the injection molding process. It is essential for producing high-precision plastic parts.
Injection molds also ensure good plastic parts’ consistency, high efficiency, and low consumption.
The injection mold gives plastic parts their complete configuration; accurate size is essential to the injection process.
Improvement of the injection mold’s service life is related to injection efficiency. The injection mold parts have a more complex structure, a unique shape, and surface loss.
Only the mold materials are currently being relied on, and the traditional mold hardening process is still complex.
Laser surface treatment technology has a wide range of applications in plastic molds. Its quenching surface hardness is very low, deformation is minimal, wear resistance and tensile ability are better, and the injection mold life is dozens of times that of ordinary quenching.
Laser surface treatment is low cost, no cooling medium and supporting devices, the treatment process without pollution of the environment, is an environmentally friendly green processing technology, will be one of the methods to extend the life of the injection mold.
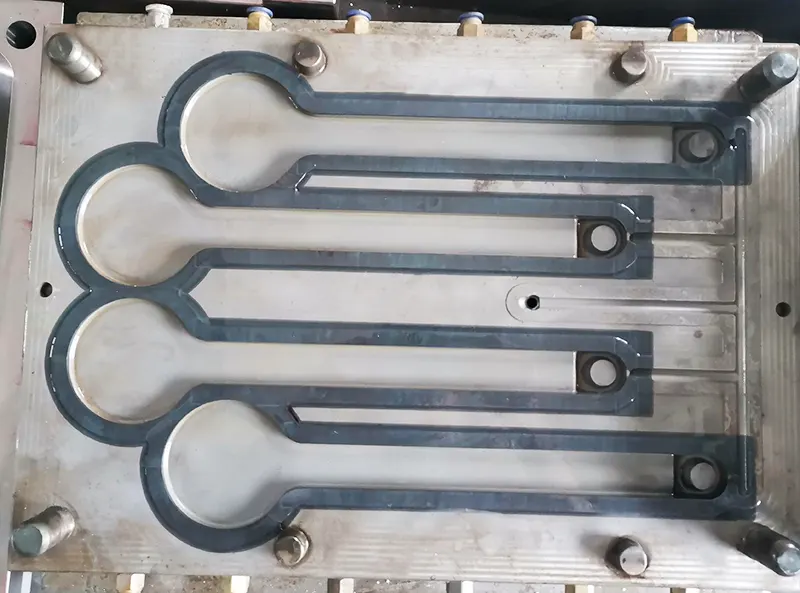
Injection mold surface laser treatment to explore
Mould surface laser treatment mechanism
(1) Explore the working principle of laser.
Laser mold surface treatment methods are Laser transformation hardening LTH, Laser surface coating and alloying LCS/LSA, Laser surface melting LS), Laser shock hardening LSH and so on. hardening LSH, etc.
This paper focuses on using laser phase change hardening surface treatment for injection molding.
Laser phase change hardening, or laser quenching, involves laser irradiation on the metal surface. The laser rapidly heats the surface, bringing it quickly to the phase change temperature.
This causes the formation of an austenitic structure on the surface. Once the laser moves away, the metal’s inherent heat conduction properties take over.
This results in “self-cooling quenching,” allowing the surface to transform into a martensitic structure.
The goal of this process is to achieve the effect of quenching.
There are three types of surface quenching equipment: CO2 lasers, semiconductor lasers, and YAG lasers. CO2 and semiconductor lasers are used for surface quenching large parts, and YAG lasers are used for surface quenching non-ferrous metals and small parts.
Laser selection factors include output power, speed of light diameter, light configuration, optical pulse width, and pulse frequency.
Laser quenching equipment crossflow CO2 lasers have a fast flow of working gas through the discharge zone perpendicular to the optical axis to maintain a low gas temperature in the chamber, ensuring high power output and a multimode beam output pattern.
The laser has a discharge chamber, heat exchanger, fan system, optical resonance cavity, inlet and outlet deflector, laser power supply, gas charging and discharging system, vacuum pump, ballast resistor box and control box and other components.
When the laser is running, the gas in the vacuum pump cavity is first emptied. Next, the working gas is filled into the filling system according to the specified proportions (N₂:Ar:CO₂ = 8:7:1) and a certain air pressure.
Afterward, the fan and high pressure are turned on. The fan in the laser body helps the working gas flow transversely through the electrode intermediate airflow channel.
Finally, a DC voltage between the electrodes induces the working gas to form a glow discharge.
After the working gas passes through the discharge area, it enters the heat exchanger to implement cooling, and re-enters the discharge electrode, and has been the cycle, which can maintain the normal work of the laser.
Laser output beam power stability and control are prerequisite requirements for laser processing, operation, and scanning with the light gun on the laser to stabilize the output power; laser pointing plays an important role in the stability of the light gun, which has a direct impact on the quality of laser processing.
The optical resonant cavity is a key component in the processing equipment. In the operation of a CO₂ laser, various environmental interferences can affect the system.
These interferences cause the laser resonant cavity to produce some aberrations. This aberration directly impacts the laser’s output power and is a crucial factor affecting the beam quality.
A Programmable Logic Controller (PLC) is commonly used to regulate and monitor the resonant cavity output lens.
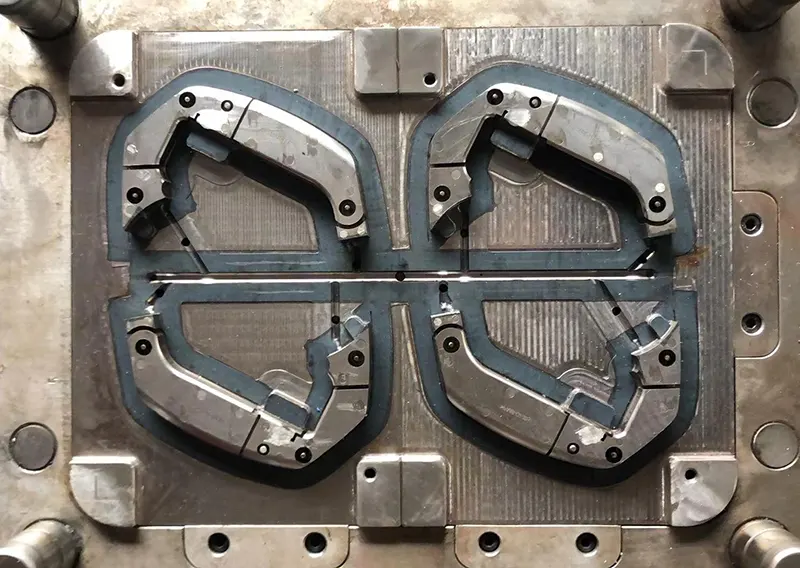
Generally, a PLC (Programmable Logic Controller) can be used to adjust and monitor the output lenses in the resonant cavity to compensate for the cavity’s deformation and ensure the stability of the power and beam quality of the laser output in the cavity. This plays a vital role in the laser’s high-quality work.
YAG lasers are solid-state lasers based on yttrium aluminum garnet crystals (yttrium aluminum garnet with the chemical formula Y3 Al5 O15, abbreviated as YAG).
The building blocks of a YAG laser consist of the laser working material, the pump source and the resonant cavity. Due to the different types of activation ions doped in the crystal, different pump sources and pumping methods are used.
Different structure resonant cavity, different other functional structure devices.
Its working principle involves using a high-energy laser pulse to apply localized heating to a small area on the material’s surface.
The energy from the laser radiation is transferred inward through heat conduction, allowing it to diffuse into the material. As a result, the surface of the material is heated or melted.
This process enables applications such as surface quenching, welding, or cutting.
A semiconductor laser is a device that generates laser light through the stimulated emission effect in a semiconductor material acting as the working medium.
The principle of its operation involves exciting the semiconductor material to a certain level. After excitation, a population inversion of non-equilibrium carriers is achieved either between energy bands or between energy bands and impurity energy levels.
Once this population inversion occurs, many electrons and holes recombine. This recombination process triggers stimulated emission, resulting in the generation of laser light.
The excitation mode has electric injection, a broad pump type, and three kinds of high-energy electron beams 3 kinds.
(2) Laser surface treatment profile.
Laser surface technology can promote the use of low-grade materials modified into high-performance surfaces, better integrate low-cost manufacturing parts and high-performance work surfaces, and obtain better economic and social benefits.
Laser hardening surface treatment is the use of the base material heat conduction for self-cooling quenching. The treatment process does not require the use of cooling media and supporting devices, processing costs are relatively low, and no pollution of the environment.
The surface hardness of laser surface-treated parts is 15%~20% higher than that of ordinary quenching.
Hardening depth is generally 0.5 ~ 0.6mm; conditions can reach more than 1mm. The laser quenching heat-affected zone is small, quenching stress and deformation are small, and a small subsequent processing allowance.
Laser output laser beam energy is continuously adjustable and controllable. The advantage of the CNC system is that the laser can be used for parts with complex shapes and difficult to deal with. The local position can be hardened, that is, different parts of the parts can be used for laser treatment.
Due to its better processing characteristics, laser surface treatment is suitable for conventional hardening treatment methods.
However, it is difficult to solve the problem of parts or the local position of the surface hardening treatment.
Main Failure Forms of Injection Molds
The main molding surface parts in plastic molds are the convex mold, cavity, concave mold, core, inserts, molding rod, etc., which form the cavity part of the plastic mold and constituting a variety of surfaces of the molded plastic parts.
The mold surface is in direct contact with the molten plastic melt, repeatedly subjected to pressure, speed, temperature, friction and corrosion.
Mold surface working condition is at 200 ℃ ~ 340 ℃ temperature (individual material temperature is also higher), mold cavity surface bearing pressure of 40 ~ 140MPa, closed mold pressure of 80 ~ 300MPa, its specific parameters and engineering plastics types.
The specific parameters are related to the type of engineering plastics.
The working conditions of the surface of the injection mold have unique characteristics:
① Plastic melts under a certain amount of pressure. The melt flows back and forth within the mold cavity, leading to friction and scouring of the mold surface.
As the plastic part solidifies and repeatedly moves in and out of the mold cavity, it creates additional friction. This continuous friction causes wear and tear on the mold surface.
Plastics containing mineral fillers or fiber fillers, such as silica sand, titanium dioxide, basalt fibers, glass fibers, carbon fibers, etc., the friction wear is more intense and prominent;
② The mold operates under conditions of large temperature fluctuations. The melt temperature typically ranges from around 200 ℃ to 340 ℃.
Due to the mold temperature control system, the mold experiences both heating and cooling effects during operation. The plastic cools and hardens at a general temperature range of 50 ℃ to 140 ℃.
As a result, the mold surface is repeatedly subjected to cycles of heating and cooling. These cyclical temperature changes lead to stress concentrations, which can cause thermal fatigue cracks.
Additionally, the cavity surface is subjected to high-pressure melt tension during the mold filling and pressure holding stages.
Cooling and demolding, the mechanical load is cyclic changes, usually a larger mold force, easy to fatigue cracking, rapid temperature changes, easy to thermal fatigue cracking, the mold will produce cracking;
③ in the injection molding containing chlorine atoms or fluorine atom materials, such as polyvinyl chloride, fluorine plastics, etc., thermal decomposition of HCI, HF and other corrosive gases such as erosion, will corrode the surface of the mold cavity.
Mold surface typical failure forms of abrasive wear, thermal fatigue cracks, scratches, deformation and corrosion.
Ultimately, the plastic parts are reflected in the plastic parts.
A variety of factors will affect the shape, size, and surface quality of the plastic parts. Mold failure will make field production control difficult, as you have to replace the mold surface parts, and will also cause greater economic losses.
Therefore, it is important to choose the right mold material and laser hardening surface treatment to extend the mold’s life.
Injection mold surface laser treatment case
Pre-hardened plastic mold steel (P20)
P20 (U.S. grade) is a pre-hardened plastic mold steel (equivalent to Chinese grade: 3Cr2Mo).
Material factory hardness 30 ~ 42HRC, with good machinability and polishability, is one of the commonly used materials for plastic mold cavity core, the composition of the quality fraction % C (0.28 ~ 0.4), Si (0.2 ~ 0.8), Mn (0.6 ~ 1), P (≤ 0.03), S (≤ 0.03), Cr (1.4 ~ 2), Mo (0.3 ~ 0.55) Ni (0.05~0.10).
Plastic molds are used more in automotive parts. In molding production, the internal parts of the mold wear, and the release of harmful gases causes mold surface damage or even surface failure.
To prolong the service life of the mold, the surface pretreatment method is often used to improve the surface performance of the mold, but the effect is not good. Wang Jianjun and other applications of laser quenching on the P20 steel surface treatment.
The results show that:
P20, in the laser quenching before the normalizing treatment, the matrix has been decomposed pearlite organization. After laser quenching, P20 steel organization presents needle martensite and lath martensite.
The laser power is 1,600W, 1,700W, and 1,800W, and the corresponding quenching temperature is 850℃~900℃. As the laser power is increased, a coarsening of the martensite occurs;
After quenching, solid solutions of (Cr, Fe) and (Mn, Fe) were formed. This resulted in solid solution strengthening of the material.
The hardness of P20 steel after laser quenching was significantly improved. The maximum hardness reached 520 HV, which is equivalent to 50 HRC.
Before quenching, the hardness was 245 HV. The depth of the quenched and hardened layer was measured to be approximately 0.93 mm.
With a laser power of 1800W, the hardened layer’s wear rate is only 0.36%, and the friction factor is 0.2013. After laser quenching, P20 steel’s hardness and friction properties have improved.
Sweden ASSAB 718
The plastic mold steel (equivalent to the Chinese grade 3Cr2NiMo) has excellent mechanical properties and good processability.
Its processing technology is simple and efficient. After a unique production process at the factory, the steel is pre-hardened to a hardness of 41 ~ 47 HRC.
The material is highly clean and offers excellent performance in polishing, photolithography, and hardenability. It also performs well in electroprocessing and skin texture processing.
Flame hardening can increase the material’s hardness up to 52 HRC. Many manufacturers use this method directly to produce injection molds, as it helps reduce certain heat treatment processes.
This reduction in processing steps can improve economic efficiency.
The typical chemical composition includes the following mass fractions:
Carbon (C): 0.28 ~ 0.40%,
Silicon (Si): 0.20 ~ 0.80%,
Manganese (Mn): 0.60 ~ 1.00%,
Molybdenum (Mo): 0.30 ~ 0.55%,
Chromium (Cr): 1.40 ~ 2.00%,
Nickel (Ni): 0.80 ~ 1.20%.
718 Mold Steel
A factory processes automotive brake handles by injection molding. The material used for the mold cavity is 718 die steel, and the injection material is glass fiber reinforced polycarbonate PC + (15%~20%) GF.
The mold has been opened approximately 320,000 times. The main failure mechanisms affecting the mold surface include cavity surface wear and deterioration of the mold surface finish, such as an increase in surface roughness.
Additional issues arise during the handling of products for post-processing, making it difficult to ensure the quality of plating or sprayed surfaces. Overall, the mold surface failure is considered serious.
The engineers used a YAG solid laser to strengthen the surface of the mold.
The results show that:
With laser power and spot diameter maintaining a constant, wear quality loss increases with the increase in scanning speed, first increasing and then reducing. When the scanning speed is 6.5mm/s, the material’s wear resistance is the best.
Hot work mold steel (H13)
H13 (equivalent to the Chinese brand 4Cr5MoSiV1) hot work die steel has excellent resistance to high temperature wear performance, the composition of the mass fraction % C (0.38 ~ 0.45), Cr (4.75 ~ 5.50), Mo (1.10 ~ 1.75), V (0.80 ~ 1.20), Mn (0.20 ~ 0.50), Si (0.80 ~ 1.20) P (≤0.030), S (≤0.030).
H13 steel is commonly used in die casting molds, forging molds, and more.
The study shows:
To ensure that the material’s surface does not melt, the depth of the reinforced layer is directly proportional to the laser power and inversely proportional to the scanning speed.
Quenching zone microstructure and properties are gradient changes; the hardened zone grain is refined, and there are twin subcrystalline organizations that appear.
Strengthening layer depth up to 1.0mm, a surface hardness peak value of 850HV0.3 (850HV ≈ 65.6HRC, 0.3 on behalf of the hardness test pressure value) appeared in the second surface layer.
The average microhardness can be increased by about 25%. High-temperature wear resistance increased by 3 to 5 times, and corrosion resistance increased significantly.
Visible laser surface quenching is an important final treatment process for mold production, enhancing the H13 steel surface hardness, high-temperature wear resistance, and corrosion resistance.
Medium carbon tempered steel (45 steel)
45 steel is one of the most commonly used medium carbon tempered steels.It has good toughness and plasticity, along with high strength and relatively low cost.
Because of these properties, it is widely used as plastic mold steel.
It is generally used to make most mold frames, and can also be used for molds that do not require high-performance cavities or cores.
The composition of the mass fraction % C (0.42 ~ 0.5), Si (0.17 ~ 0.37), Mn (0.5 ~ 0.8), P (≤ 0.035), Ni (≤ 0.25), Cr (≤ 0.25), Cu (≤ 0.25).
Some experts and others used laser power P = 3,200W, scanning speed V = 1.2m/min and V = 2.5m/min CO 2 laser machine to harden 45 steel surface.
The results show that the laser-hardened layer consists of three parts: the surface fusion zone, the homogeneous phase change hardening zone, and the transition zone.
The corresponding organizations are lamellar martensite, which is fine and homogeneous, cryptocrystalline martensite near the surface melting zone, mixed martensite, quartzite, and partially unmelted ferrite.
Increased hardness of the laser hardened layer compared to the original substrate, the highest hardness occurs in the subsurface layer with a hardness of 1050.3HK, about three times that of the substrate.
Laser quenching improves the corrosion resistance of 45 steel, with the increase in tracing speed and enhances the corrosion resistance. Zou Guangkun et al. application of 5kW CO2 laser on the normalized state 45 steel surface laser quenching.
Tests show that:
Laser treatment of the hardened layer profile organization is divided into a fully hardened zone (ultrafine needle martensite), an incomplete hardened zone (martensite, ferrite, and pearlite), and a high-temperature tempering zone (tempered sostenuto). Laser hardening increases the hardness of normalized 45 steel.
Conclusion
In recent years, laser surface technology has developed greatly, the application field is gradually expanding, and laser surface treatment process research has reached the stage of industrialization.
Laser surface quenching has unique advantages in the injection mold has been applied, is to extend the service life of the injection mold is one of the important ways.
After laser treatment of the surface, thermal fatigue cracks, scratches, deformation, corrosion, and other problems can be solved. This effectively extends the mold failure time and can reduce costs and increase efficiency.
We firmly believe that laser processing will continue to advance with the in-depth study of laser theory and technology.
By empowering laser processing with intelligent digital technologies, and integrating diversified laser processing modalities into a single service for mold processing, the overall capability will be significantly enhanced.
In the future, laser processing equipment will achieve greater accuracy and stability, reduce costs, and play a vital role in the field of mold processing.
.