Rotary two Color Mold Design
Ordinary injection molding machines can usually only produce plastic products of one color in the production and manufacturing of molds, not two-color injection.
While two-color injection molding refers to the injection of two different materials into the same pair of molds, the general method is to use two injection molding machines or a two-color injection molding machine to achieve the injection molding process formed by two materials.
Here we take a product as a real example to illustrate how two-color injection is realized.
Product Description
As shown in Fig. 1, this plastic product is made of PP. Its external dimension is 41×41×36.68mm, and the average wall thickness is about 3.1mm.
This is a small plastic product with threads and other inverted buttons. It is the finished product of the first injection, which is also a one-color mold.
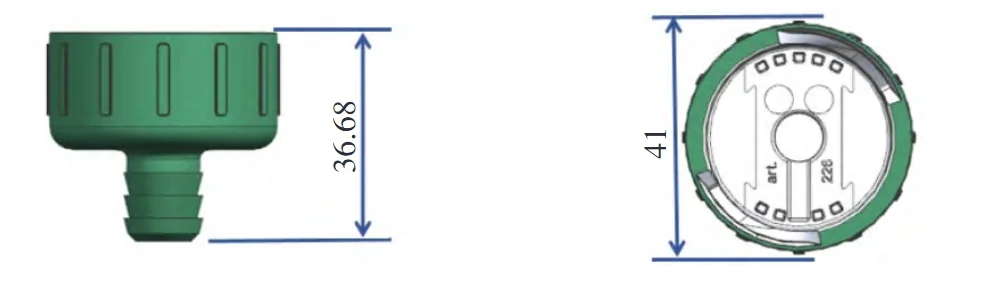
Since the black inner ring of this part is TPE, a second injection is needed. As shown in Fig. 2, the second injection molding part is an inner ring with a height of 6.56mm and an outer diameter ϕ32.29mm, which is close to the inner wall of the first injection molding part to form the required finished product, and the cavity is arranged as a 1-mold 2-cavity.
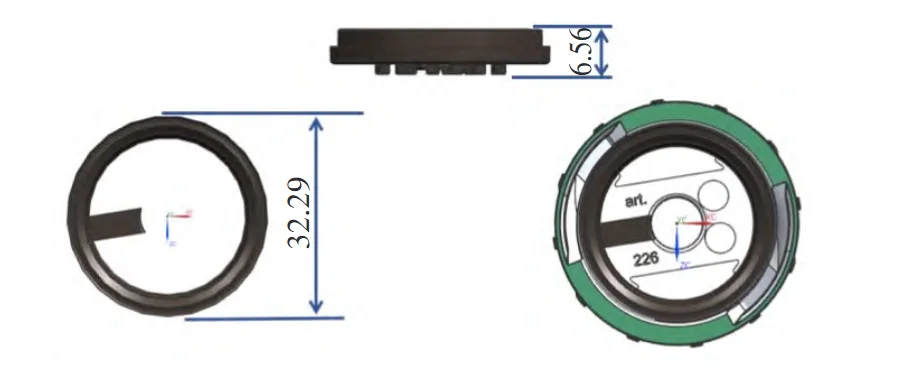
Key points of product design
The design of the cover and shell is based on the conventional parting surface, as shown in Fig. 3. The inner slider of the fixed mold was adopted because it needed to cooperate with the rotating movable mold plate and the demolding of the inverted buckle.
The inner parting of the cover and shell is completed by the fixed mold slide and the fixed mold insert, and the moving mold slide completes the outer parting to achieve the inner and outer parting, as shown in Fig. 4.
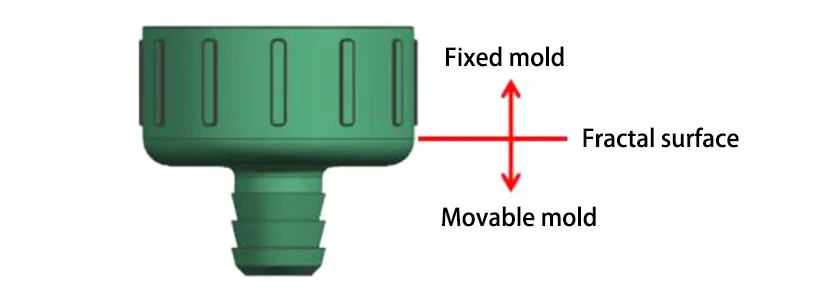
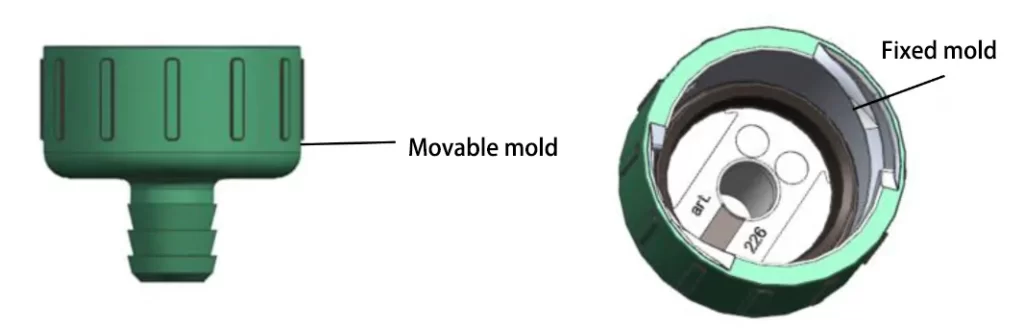
Mold structure design
Rotary inner mold design
To realize that a single ordinary injection mold can inject a two-color mold, the structural design of a rotating inner mold must be used. A set of rotary shaft systems is designed to realize this function in this set of molds.
The overall process is to drive the movement of the rack through the cylinder, which drives the rotation of the gears and the rotary axis, so that it is rotated 180 ° at the time of the two injections and opening of the mold respectively, to achieve the first injection of products for the second injection, to complete the production of two-color mold manufacturing.
In the next molding cycle, the rack will move opposite to the previous movement under the cylinder’s drive, ensuring the stability and continuity of the inner mold rotation.
At the same time, to prevent interference and accurately control the rotation of the inner mold, all the templates except the inner mold of the product are avoided, completing the drive of the whole set of rotary axis systems. The overall design structure and rotation process are shown in Fig. 5 and Fig. 6.
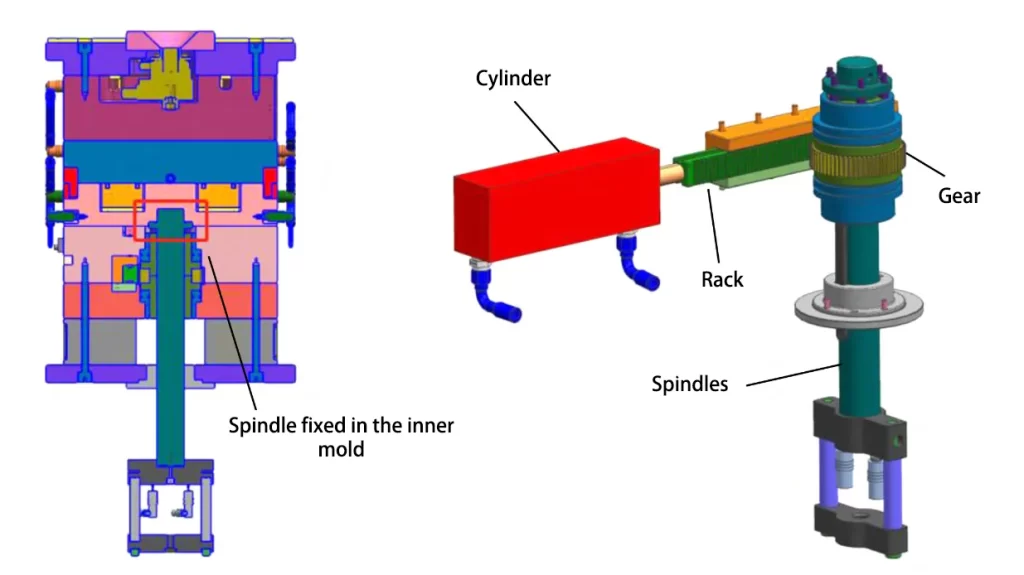
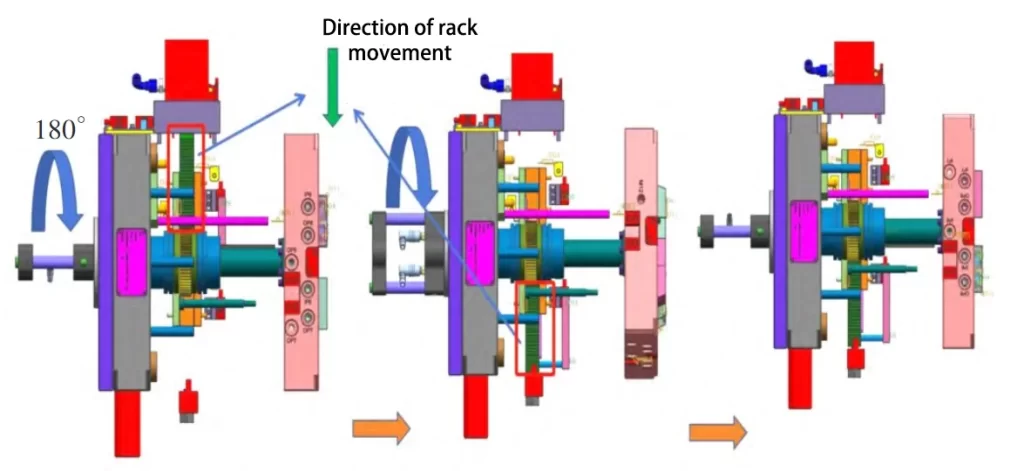
In the design, to cooperate with the rotation of the inner mold, the overall style of the inner mold should be the same as the first color and the second color, when the first color is injected, the product stays in the slider of the inner mold, and when the rotary table on the injection molding machine rotates 180°, the second color will be produced, and then continue to enter the next mold molding cycle after completing the finished product.
The overall pattern of the inner mold is shown in Figure 7.

Dual Chirp Design
In order for the rotary axis system to cooperate and thus realize the production of two-color molds, two sets of sprue on one mold must be designed.
As shown in Fig. 8, in addition to the main sprue on the original panel, another secondary sprue is designed on the sky side of the same mold to match the design of the double cavities, so as to complete the two-color injection.
The main sprue is the first color injection nozzle and the secondary sprue is the second color injection sprue. During the injection process, two sets of injection systems work simultaneously by adding injection device to the injection molding machine to improve the production efficiency.
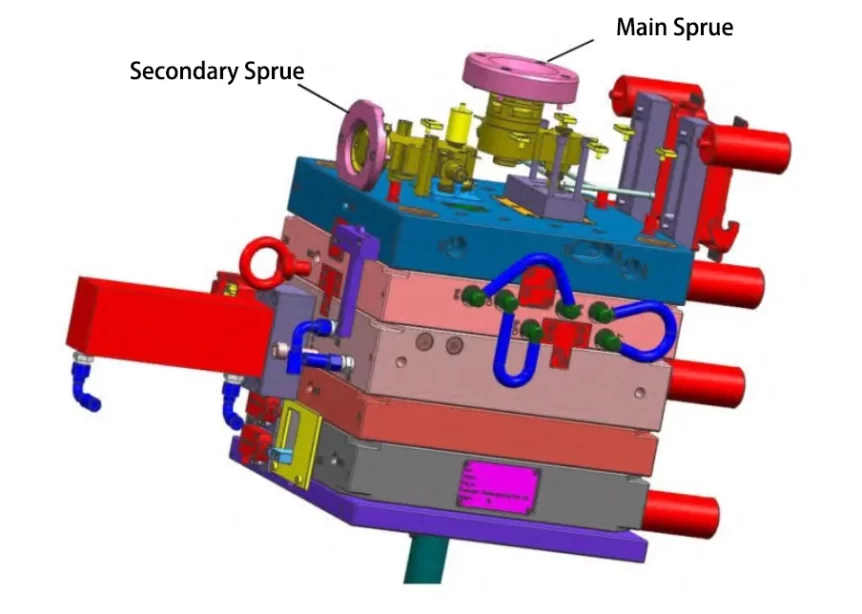
Parting Design of Slider Inserts
By designing the slider and inserts for the product to be parted, the first color in the slider part of the moving mold is not designed to protect the product from being touched by the slider, so the slanting guide pillar is not designed.
This prevents the product from being damaged when the mold is closed after it is opened and the slider is moved. However, the second color is designed with a slanting guide column, making removing the product convenient after manufacturing.
Moreover, by adding a spring and a block structure at the intersection of the slider’s oblique guide pillar, the problem of the oblique guide pillar being touched when the mold is closed by the second injection is solved.
The slanting guide pillar is also processed with the corresponding fitting position, which is convenient for fixing the slider and avoiding bruising. Finally, when entering the next molding cycle, the slider that moved after the second injection is returned to its position by the slanting wedge.
The structure of the moving mold slide is shown in Figure 9.
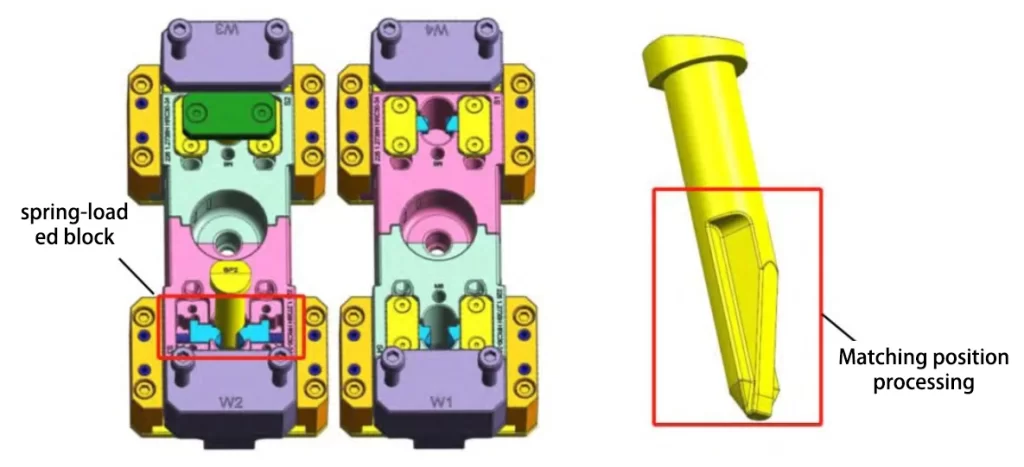
The fixed mold slide and hot runner insert are used to part the product and complete the second color injection internally. To remove the product’s internal threaded buckle, the fixed mold slide is only made at the first color, and the second color relies on the hot runner insert to complete the second injection.
When opening the mold, through the design of the stroke screws, the hot runner inserts are first drawn 17mm, and the fixed mold slider can make the product detach from the internal backlash due to the principle of shrinkage to complete the molding of the first color product. As shown in Fig. 10.
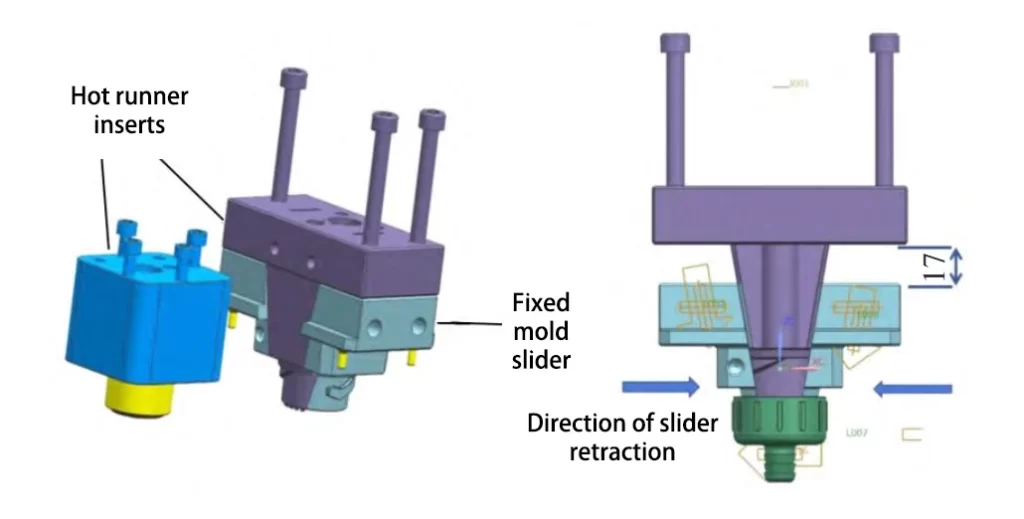
Whole process of rotary inner mold two-color molding
The first step is to open the mold. The first step is to open the fixed mold by 17mm, and the first color hot runner insert first pumps the fixed mold slider inward, and the molded part will be detached from the internal inverted buckle, as shown in Fig. 11.
The second step is to open the mold. The moving and fixed molds are entirely separated, and the parting of the fixed and moving molds is completed, as shown in Fig. 12.
The third step is to rotate the inner mold. Firstly, the injection molding machine and the rotary axis push the inner mold out 100 mm, and then the cylinder drives the rack and pinion to rotate it 180°, as shown in Fig. 13.
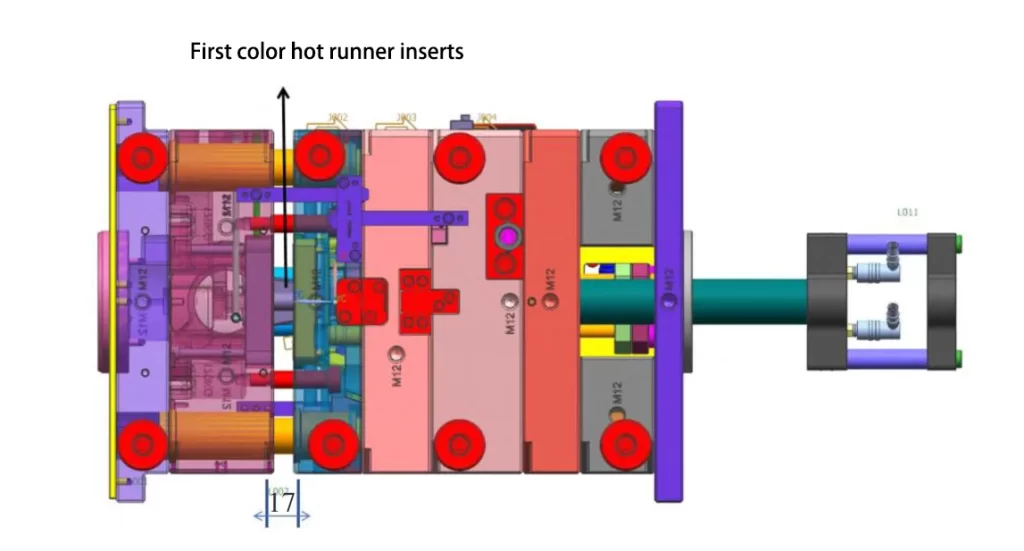
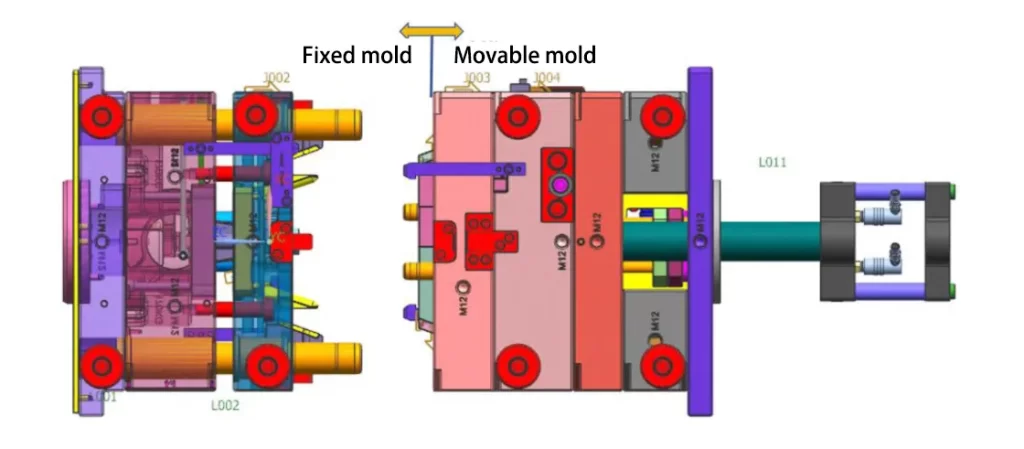
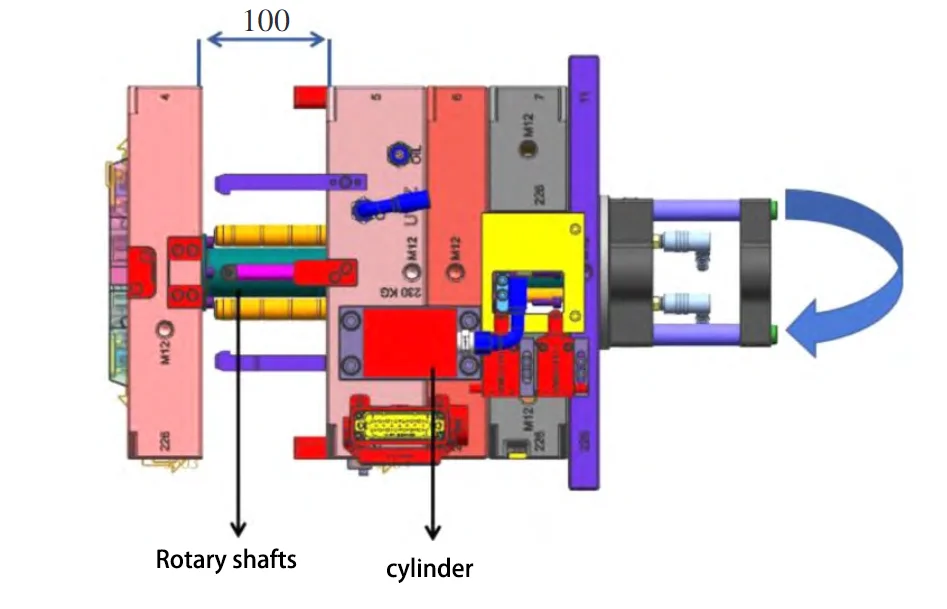
The fourth step is to close the mold. After the injection molding machine and the rotary axis reset the inner mold, it is reset with the fixed mold to complete the mold clamping and start the second color injection, as shown in Fig. 14.
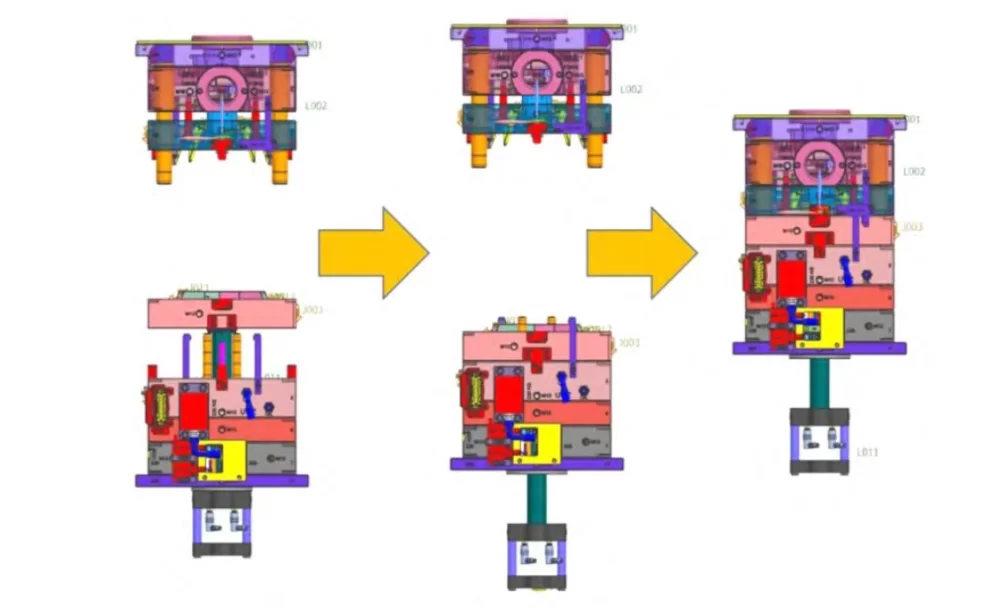
The fifth step is to open the mold. At the same time as the second step of mold opening, the slider at the second color is driven by the inclined guide column to detach from the molded part, and the product is detached from the appearance of the undercut, as shown in Figure 15.
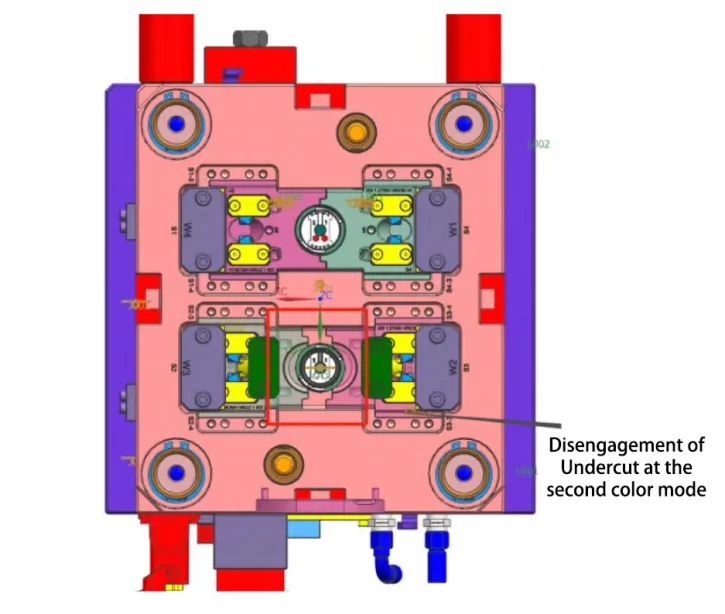
Step 6: Eject the product. After the injection in the second step and before the rotation of the inner mold in the third step, the cylinder actuates the ejector plate, which drives the ejector rod to eject the finished product.
After the inner mold is rotated and reset, the ejector rod is reset again, and finally, the moving and fixed molds are reset to complete the mold closing. The first and second colors continue to start the injection work, as shown in Fig. 16.
The first and second colors will continue to start injection work, as shown in Figure 16.
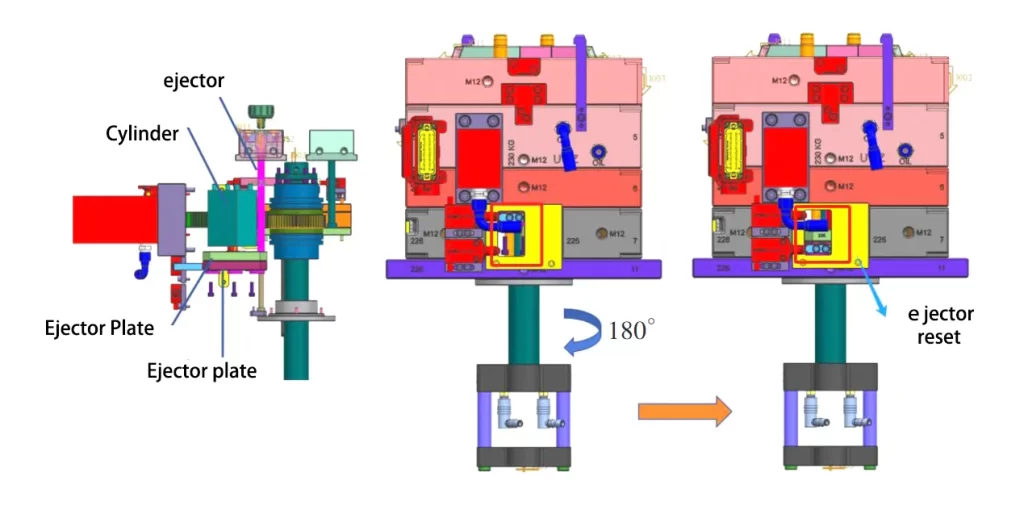
Because the fifth step and the second step are synchronized, and the sixth step is also included in the fourth step, when the mold is completed in the fourth step, it will enter the next repetition of the action and the next molding cycle.
Summary
When designing and producing two-color molded parts, this mold innovatively uses the structure of a rotary moving template.
This successfully solves the pain point of traditional two-color mold production, which requires a special two-color injection molding machine or two injection molding machines. It improves production efficiency and reduces the cost of the machine, achieving the plan of cost reduction and efficiency.
At the same time, through the analysis of the plastic parts in the pre-design stage, the slider and insert for parting are adopted, which better matches the rotary inner mold and the structure of double nozzles. Thus, the mold can be successful in one trial run to reduce manufacturing costs and improve product quality.
The structural design of the rotary inner mold and the parting design of the two-color mold can be promoted as the mold design scheme for two-color molded plastic products.